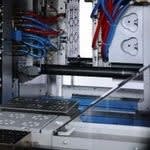
They introduce their new concept „Sigma Inside“ which raises the bar for productivity and seamless quality control. Parts, which normally gravity drop are removed by high speed take out robots and placed in containers according to their cavity number. The modular concept allows the user to configure the system to his specific needs to ensure transparency in the QC process and traceability throughout the supply chain. The results from the first installation show a 30% increase in productivity.
Hekuma has cleared the air once and for all that utilizing a robot to remove normal „drop parts“ is a cycle time killer. The fact is that a servo controlled take out device can actually allow for shorter mold open time without the danger of mold damage. For free falling ejection, a certain “safety margin” must be included in the mold open time and closing speed.
During the removal, integrated sensors confirm that a complete shot has been removed to ensure no parts are lost and more importantly that no parts remain in the mold which may result in costly damage and related downtime. Once the automation has control, the real task of „Sigma Inside“ begins. The cavity specific handling and maintaining integrity through the process allows the user nearly unlimited possibilities.
Parts removed can be kept completely separated throughout the production and handling process allowing for complete traceability even to the cavity level. In the event of an “undetected” issue with one specific cavity, parts of the affected cavity can be rejected or recalled to minimize liability.
If a defect regularly appears in one specific cavity, the cavity can be potentially shut off or systematically rejected without the need for unplanned downtime for mold repair. With „Sigma Inside“, parts out of the allowable specification can be so designated and placed in the appropriate container for disposition. Production can continue uninterrupted until such time as the mold repair plan can be analyzed and implemented in a logical manner.
„Sigma Inside“ allows the user to manually remove a quality shot from the QC sample station for periodic testing. This ensures that the parts for the quality testing all come from the same shot and the parts are associated with the right cavity.
This concept can also be expanded to include the possibility of a vision inspection system for complete quality control and documentation. In the event that the same cavity is repeatedly defective, the cavity can be shut-off using the appropriate algorithm.
Utilizing the automatic sorting and shot count information will allow for easier implementation of a scientific “DOE” (Design of Experiments) in order to determine not only allowable process tolerance levels but also to facilitate a planned mold maintenance schedule.
„Sigma Inside“ is highly flexible and can be used for a wide variety of applications. This is where the application specific Quick-Change parts come into play and the integrity of the cavity specific sorting is maintained. The modular design of the handling and tooling allow for extremely fast and efficient changeover times. Because of the cavity sorting, it is absolutely conceivable that “family parts” could be produced in the same mold but still maintaining the integrity for packaging and shipment.