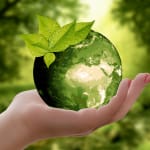
On the occasion of Plast 2023, the most important Italian event of the sector, Moretto will participate with a stand of 400 sqm at the edition scheduled from 5 to 8 September in Milan. The fair will give the opportunity to know the evolution in the world of plastics processing, a sector that is facing a phase of radical change due to new technologies, renewed consumer trends and the needs of an ever-evolving market.
Energy efficiency such as a engine development
One of Moretto's strategic development drivers is energy efficiency guaranteed through its products. A long journey in which the awareness of customer needs, the company's commitment and the development of the necessary technology have combined perfectly to create a virtuous path that has led to innovative solutions, in line with the needs of the current economic context. The manufacturing industry sector has among its highest costs the electricity, and equipping itself with solutions capable of significantly reducing these costs is an indispensable competitive advantage.The OTX hopper is the result of sophisticated mathematical simulations that allows the analysis of the geometry, fluid dynamics, thermodynamics and material flow of the plastic granule with the support of the super computer Leonardo, an exceptional computer capable of 22 trillion operations per second. OTX ensures a regular material flow, guaranteeing correct drying of each individual granule being processed. In addition, the optimisation of the process parameters has enabled the hopper , technological airflow and treatment time to be reduced by 40% for the same hourly output. The reduction of hopper has been possible by the energy efficiency of OTX, which improved by 66% at the same production capacity. Because OTX is not a simple hopper but a concentrate of 7 patents that ensures a perfect execution of the drying process with full control of all working parameters. OTX can be considered a 'Hopper Machine' in its own right by virtue of its features.

The revolutionary OTX hopper (Original Thermal eXchanger) developed by Moretto.
But the advantages don’t finish here. The use of a smaller hopper allows the application of a smaller dryer. Moretto has developed the HYPER FLOW turbo project capable of generating up to 2,400 mc/h of technological air with the aim of creating a machine capable of using as little energy as possible. As an example, the HYPER FLOW version, available on 17 models, is a revolution of dryer project on the 800 series and the entire X Dryer 20 series range. A 1,200 mc/h generator with side channel pumps in continuous operation consumes 16.5 kW/h. A HYPER FLOW turbocompressor for the same performance consumes 4.8 kW/h, guaranteeing energy savings of 11.7 kW/h and economic savings of € 35,800 per year. This is just the last part of a project development and innovation that have covered over 32 years which can be summed up as following:
- X Technology
- No water for cooling
- Electrical movememt of the exchange valves
- Total energy recovery
- OTX Hopper
- Moisture Meter
- Hyper Flow Turbocompressor
Leonardo Cluster has contributed to this energy efficiency challenge by enabling us to offer customers’ solutions that are indispensable for all companies. Tangible energy efficiency that frees up significant resources for development and growth.