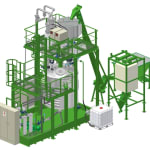
H&S Anlagentechnik has developed a new reactor type (MP = multi-material to polyol) for medium sized amounts. The new MP reactor is designed to produce 500 to 1000 tons of polyol per year and for the first time makes it possible to synthesize various raw materials to APP (aromatic polyester polyol) in one system.
The new compact MP reactor module can be integrated one or more times into a system design to produce the required amounts most economically. This mid-sized MP reactor needs very little space, is delivered as an operational module, and is more economical than conventional systems due to lower manufacturing costs. The MP reactor thus enables a larger group of users to produce APP (polyol) as needed. Target markets are in particular emerging countries with increasing demand for PU rigid foam.
The MP reactor has a compact operating volume of up to two cubic meters, which allows pre-installation of the compact core component for shipping in a 20-foot container. This results in much lower assembly costs at the site and increased safety, as no welding must be carried out by the customer. The manufacturer specifies process time for a batch of about 10 hours.
An H&S base system consists of: material feeding module, stainless steel reactor cell, material gravimetric analysis, fractionating column, pump groups, filters, and valves, solid material delivery units, temperature management, control module (computer-based), assembly service and training of operating personnel, recipe development using own development laboratory .
Optionally, H&S can provide tank storage technology for polyol or blending stations
The efficient use of raw materials and energy gives the system operator a cost advantage for in-house polyol production of over 30% in comparison with purchasing comparable polyol on the raw material market. This results in amortization times of less than two years. According to the manufacturer, this calculation is based on the situation in Germany assuming the nearly analogous floating of raw material prices for the materials used such as PET and sales revenues of polyol with relatively constant margins in the future.
This reactor type is even more economical for emerging economies, as cost factors such as wages or energy may be even lower. It should also be considered that there are no transportation costs or import duties for importing raw material. An additional factor is that recycling locally entails no fluctuations in exchange rates or need for foreign currency. In general, processors are independent of raw material suppliers. H&S sees areas for the use of rigid foam in insulation (white goods/pipe in pipe), the construction industry (sandwich panels/spray foam), the automotive industry, and in the decorating/coating sector.
Due to the positive basic properties of the raw materials, the highly pure APP produced in these systems offers PU rigid foam processors a few advantages over conventional polyol – integrated flame retardant, very low acid levels, significantly higher storage stability of the polyol, lower density of rigid foam (up to 5% material saving), better insulation value (heat coefficient/insulation factor), and at least 20% greater compressive strength of rigid foam made from the polyol. The result is an economical alternative for mid-sized needs.
In addition, H&S Anlagentechnik also offers the corresponding large system technology for much greater annual requirements of over 1,000 tons per year as well as pure PET reactors. The third reactor type H&S offers is a PU reactor that breaks down PU waste at the PU processor to polyol in order to re-introduce the material into the cycle.