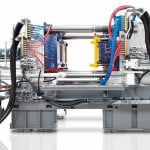
Sophisticated 2-cavity mold
Transport packaging manufacturers in South Africa are experiencing increasing cost pressure. The main reasons for this are primarily the continuously increasing raw material prices and fixed costs such as those for wages and energy. The requirements for the new injection molding machine and mold technology at the Johannesburg location were correspondingly high. MCG decided in favor of using a new, sophisticated 2-cavity mold and selected the suitable injection molding machine. The partners in this project were mold makers Schoeller Allibert and KraussMaffei, who provided the suitable injection molding technology. The goal: More output at lower cost without sacrificing quality, durability or user-friendliness.The first milestone
First, the focus was on the mold. "We wanted the best and most productive mold there is for such applications," stipulated the guideline. This is where Schoeller Allibert came into play, known worldwide for the development of innovative reusable packaging products. The bid entailed a mold with two cavities – a similar mold was already being used to make transport crates for beer and brewery products. The market share of MCG in this segment is now to be expanded significantly with the first use by a manufacturer of milk crates.This mold form combination was the first milestone for MCG. Due to the high requirements, a special injection molding machine was needed that went beyond the usual specifications. KraussMaffei fit the bill perfectly with a large MX 1000-17200 machine. In terms of the two-cavity mold, this injection molding machine offers optimal utilization of platen dimensions and clamping forces with an excellent price/performance ratio. On-site service and a training concept for every employee involved, from the operator to the project manager, proved to be another important factor in the decision.
The target-oriented solution
Selected technical components supported MCG's requirements with regard to shorter cycle times and low energy consumption. This led to choices such as the HPS barrier screw being installed in the MX machine, providing exceptionally high throughput with excellent melt quality and allowing shorter cycle times, and a 20 percent lower energy consumption as a result. The insulating sleeve around the injection unit offers even more potential for saving energy. It reduces the heat-up time by 20 to 30 percent. The total heat energy required drops by 20 to 40 percent. "Schoeller Allibert, KraussMaffei and its South African representative, P&CT, developed a solution perfectly tailored to our requirements. We were amazed at how effectively they worked together," says Ian Victor, Managing Director at MCG. The combination of a precisely configured machine and a high-tech mold allows us to realize a wide variety of tasks simultaneously, such as short cooling times without warpage or sink marks. And all on two cavities."This required a very uniform melt and a very short injection time. The machine from KraussMaffei played a significant part in making this possible," says Stefan Scheuerer, Director Sales Africa for Schoeller Allibert, in lauding his project partner. The success could be readily measured. MCG had specified a cycle time of 30 seconds, quite a challenge for the product size (424 x 334 x 310 millimeters). At machine acceptance, KraussMaffei was able to run a stable process at a cycle time of 28 seconds. The investment has already paid off. Three identical systems just like this one are now successfully producing crates at MCG's Johannesburg location.