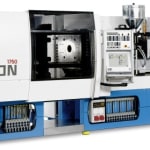
On show is Netstal's ELION machine which is by now perfectly established in the market. An application from the area of thin-wall injection moulding demonstrates effectively how well the models of this all-electric machine range perform. In its participation in the Interpack Netstal also picks up two mega trends in the plastics trade.
An application from the packaging sector on an ELION 1750 demonstrates the high efficiency of this range of all-electric machines. The product is a container holding 500g, moulded at a cycle of less than 4 seconds in a 2-cavity mould made by the Steiert company of Germany.
The packaging article in question is made of a polypropylene of the Basell company and is provided with a label during the moulding process by IML (In-Mould-Labelling). Inserting of the labels and removing of the products are accomplished by a handling device of Messrs Ilsemann, Germany, while feeding of the raw material is in the care of Motan, also of Germany.
Ecological aspects such as noise, emissions and energy savings are of ever greater importance to plastic processors and are fully considered in the all-electric ELION machine.
Thanks to the recuperation this energy can be used to turn the plasticizing screw for metering. In this way the majority of the energy required to drive the machine is obtained from the braking processes of the individual axes. Up to 50% of the total energy costs can be saved as a result of this characteristic, which in turn leads to lower production costs for the plastic mouldings.
The ELION, moreover, guarantees an operation free of emissions because it features a.o. a closed lubrication system of the mould closing unit as well as encapsulated and water-cooled electric motors. This makes the ELION the ideal injection moulding machine for productions in clean rooms.
At the Interpack Netstal underlines its competence in the area of processing plastics from renewable sources. Based on numerous processing and application-technical tests Netstal has gained much valuable experience in this field.
At an Info Point set up for the purpose on the Netstal exhibition stand the visitors will learn more about the significance of processing the biocompatible material polylactide (PLA) on the basis of sample products.
An environment-conscious production is possible by all means also in the area of injection moulding, starting from the selection of the raw material right to the finished article. At the world's biggest trade fair for packaging, the Interpack in Düsseldorf, Netstal presents itself with the translation of these developments that are so important now and in future.
The customers' increasing calls for extra benefits beyond the purchase of the equipment means that the services around the moulding machines become ever more important.
Under the umbrella of the service brand ?Netstal Support Concept? the specialists of the Netstal company look after the clientele around the clock, and this all over the world. This comprehensive service performance guarantees the Netstal customers an economically efficient production. Drawing from know-how and experience accumulated over many years, Netstal is in a position to offer its customers valuable support throughout any project phase.