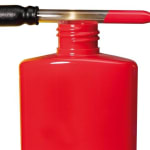
Initial testing in monolayer containers shows that these highly compatible systems allow for higher pigment loadings and lower usage rates, while practically eliminating past challenges related to screw slippage. Improved resin compatibility results in stronger weld lines in the finished container as evidenced by scores in standard burst and compression-loading tests.
“Extrusion blow molders and brand owners in the personal care and household products markets often find liquid masterbatches to be an attractive alternative to solid concentrates,” says Raymond Sloan, Head of Liquid Color, Clariant Masterbatches North America. “However, until now, use of liquid color has been limited in blow molding of polyolefin resins because many liquid based carrier systems (including mineral oil) would not incorporate well with the resins. It was pigment friendly, but not resin friendly.”
The new Clariant masterbatches use a liquid vehicle system that incorporates suspension aids and binders have been incorporated into the new LVT masterbatches to allow for higher pigment loadings and (in most cases) lower usage rates. Additional components enhance flow and make for dramatically faster color changes. These and other advances allow Clariant to offer significant functional advantages in important applications and markets.
Benefits include:
• Improved weld-line strength. Previous carriers had a tendency to rapidly bloom to the surface of extrusion blow molded containers, interfering with seam re-welding. In contrast, the new Clariant liquid products appear to actually assist in the formation of a strong seam. Finished products have easily passed industry standard top-load and drop tests.
• Better processing characteristics. The new Clariant liquid colors have a positive effect on material flow in the extruder. Reduced screw slippage leads to improved mixing and more complete dispersion and less streaking. It also results in processing temperatures as much as 17°C (30°F) lower and, therefore, less cooling is required.
• Faster Color Changes. Greater Productivity. The Clariant LVT products tend not to adhere to metal surfaces and, in fact, can act as a cleansing agent, removing deposits left behind by other colorants. Color changes that might typically take several hours with solid pellet colorants can now be completed in just minutes with the new liquid colors from Clariant. This means processors spend much less time producing scrap for regrind and more time producing actual saleable containers.
• “So far,” Sloan says, “testing has been completed in several types of monolayer containers and we are confident that similar results can be achieved in multilayer applications involving both opaque color and pearlescent effects. Although liquids have had only limited acceptance in these markets, we fully expect our new technology, along with Clariant’s industry leading technical service and global reach will allow us to discover new opportunities in the extrusion blow molding market. Clariant is actively seeking processor partners to help us test and prove LVT benefits in specific applications.”