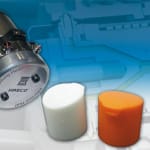
With Hasco's innovative Z10440/. Multi Shot nozzle, side gating with submarine or tunnel gates has become a thing of the past. So, too, has the increased cost of split mould inserts resulting from former hot runner solutions that increase operating and maintenance costs.
The challenge of this project was to develop a solution that makes it possible to replace individual nozzle tips from the parting plane and also ensure optimum colour change characteristics. A significant reduction in cycle time (of the existing reference mould), taking account of the high optical demands made on the finished article, was also targeted. The produced article – a pump head for a dispenser – is used in the cosmetics industry. Outstanding surface quality with minimal separation point were two key requirements.
The mould was designed and produced by Hasco. The development team from the Hot Runner Division focused its attention on the design of the nozzle and in particular on optimum, improved cooling of the inserts. The newly developed Multi Shot Z10440/ has 2, 4 or 6 individually replaceable nozzle tips. A special patented design solution for the nozzle tips and their fixing system guarantees maximum maintenance friendliness.
The tip and sealing ring are together in one segment and can therefore be easily assembled or dismantled from the parting plane, even when cold. In the event of mould damage, individual cavities can be provided with a "blind segment" and production continued from the remaining cavities without interruption and without any sorting.
Optimum cooling of the insert and elimination of the sub-runner resulted in a reduction in cycle time of around 35%. The gating point complies with the specified optical and dimensional requirements. Due to the rheologically designed runners and gentle conveying of the melt, colour change is fast and clean. To be able to execute the mould project cost effectively and efficiently, the development team took advantage of Hasco's extensive range of standard mould units – the largest in the world. Since the mould was to be designed as a production mould, use was made of hardened, wear-resistant mould plates of 1.2764. The rest of the mould structure was made from the proven Toolox33. For economical demoulding, elements from the Hasco slide element range were incorporated. Fast, accurate control and user-friendly programming were achieved with the new multi hot runner control unit Z1240/.
With this project, Hasco has demonstrated its proven product development expertise, and offers a nozzle with which direct, side gating of articles can be carried out economically and easily.