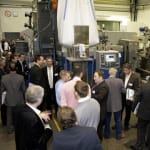
More than 150 specialists from 17 countries took this opportunity - the first ever public presentation of the Vacurema inline strapping technology - to see the line in action. The system demonstrated in a real production environment at the Open House event consists of the Erema Vacurema Basic 1308 TE, optimised for the recycling of standard bottle flakes to produce high-quality melt with virtually no IV loss, and a Techno Plastic Tight Strap 300 stretching plant connected directly to it.
Experts from around the world were amazed by the reduced costs for the input material and the enormous energy savings compared to conventional strapping systems. Specialists from Erema and Techno Plastic also gave speeches on both days on the new process and plant technologies presented for the production of high-strength PET strapping band from post consumer PET flakes.
Compared to a conventional multiple plant configuration featuring a crystalliser, drier and extruder, with the new Vacurema inline strapping technology you can save around 20 to 25% of input material costs and also reduce energy costs by more than one third - without sacrificing the quality of the end product. The tensile strength of the PET strapping with a cross-section of only 15.75 x 0.98 mm? produced during the symposium was 517 N/mm2 (embossed) which corresponds to 6,400 N (640 kg) breaking load.