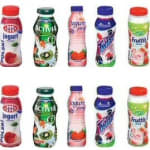
There are many varieties from the best-known multinational companies that come into the market with different positioning strategies, aimed at various consumer sectors and niches: some concentrating on the health and active lifestyle aspect, others on desserts, others still on a high quality product for adults, and finally on products for kids.
Plastiblow, the Plastimac group company producing extrusion blow moulding machines up to 30 litres, has experience of supply a wide range of machines in this field. Plastimac machines for these types of bottles differ in size and format, featuring from 2 to 24 cavities for oriented production, or up to 40 cavities with the bottom-to bottom or neck-to neck arrangements, according to the production requirement.
Among the most interesting models offered for high productivity we can consider those defined as "long stroke" models. This expression describes shuttle extrusion blow moulding machines that can host moulds with a high number of cavities with outputs that achieve several million pieces per year, once obtained only with rotary machines. High productivity with long stroke shuttle machines is made possible thanks to the technological solutions that Plastiblow were the first to introduce, such as the horizontal movement of the mould holding carriages and bouncing extruder.
This technology is becoming more and more popular as opposed to the inclined or pendulum movement of the carriage due to the several advantages it brings. In the first place, with the same mould length, the mould stroke from below the head to the blowing station can be reduced for faster cycles. Also the blowing nozzles stroke is reduced with the same advantages for cycle time. Parison cut and as a consequence, bottle neck quality are improved by the extruder bouncing avoiding the tear off effect produced by carriage movement. The choice of linear guides made by Plastiblow, is now accepted by most machinery makers, because they:
- dramatically reduce the typical maintenance problems associated with column systems
- ensure maximum stability and precision of the mould holding carriage movement,
- increase carriage speeds, thus reducing cycle times,
- minimise energy waste, since the carriage moves on rolling elements reducing slipping friction.
In most cases yogurt bottles have wide neck finishing with an annular surface for the thermo-welding of a protective peelable foil. For the best finish on these necks Plastiblow have designed a specific wide mouth cutter, that allows the complete finishing of the bottle in the machine, with important advantages for the layout and space saving in the plant. Thanks to its experience Plastimac can guarantee its customers all the necessary know-how in this field.
The new electric Plastiblow machines have proved to be ideal for the production of yogurt bottles in clean rooms or controlled atmospheres, mainly because of the complete absence of hydraulic oil that avoids any risk of contamination of both products and the environment. These blow moulding machines have been developed from the progression of an hybrid concept, initiated by Plastiblow engineers some years ago on bigger machines, which used an electric servo-driven carriage movement combined with a hydro-mechanical clamping of the mould. Plastiblow have developed this technology, taking advantage of their previous experience gained from the application of toggles and cranks for its machines’ movements.
- energy saving, because electric motors operate more efficiently and only when needed, whereas hydraulic pumps work continuously;
- improved precision and repeatability, thanks to the more accurate response; movements obtained with hydraulics are less precise because the viscosity of the oil changes depending on temperature and its degradation over time;
- higher productivity, thanks to faster dry-cycle times, constant movement and consequent reduction of faulty bottles;
- reduced environmental impact, due to the absence of the hydraulic fluid and lower noise levels.
Where high productivity is required, the ideal machine for the production of light weight yogurt bottles from 100 to 250 cc, is the PB5E/DXL that can give an output of up to 20.000 pieces per hour in bottom-to-bottom or neck-to-neck configurations.
Other applications for the drink packaging industry, such as flavoured milks or vitaminized beverages, require barrier containers with multilayer configurations or special sealed-neck bottles to protect the bottle interior from contaminations. Working side by side with several customers, Plastimac has also gained good experience in supplying many coextrusion machines with different multilayer configurations, thus being able to support customers also for this kind of applications.