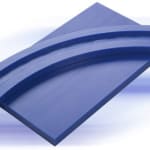
Quadrant launches new Tivar polyethylene bearing grade Tivar HPV to support improvements to the productivity and safety of conveying systems and a reduction in maintenance.
New Tivar HPV is an ultra high molecular weight polyethylene (UHMW-PE) developed specifically for wear components subject to challenging production environments, such as high speeds, high temperatures, high loads and aggressive cleaning agents. It is Food Contact compliant and available as semi-finished material and custom machined parts.
Tivar HPV has an innovative, built-in dry lubricant which gives it a Limiting Pressure Velocity (LPV) value 18% higher than competitive material, resulting in reduced pressure sensitivity for finished parts. POM-C counterplate tests by Quadrant indicate that Tivar HPV offers the lowest coefficient of friction (COF) value on the market, with a reduction of up to 80% in comparison to other UHMW-PE materials.
As a result, components made with Tivar HPV show improved sliding behaviour and high wear and abrasion resistance. This avoids excessive wear and deformation of parts to support the longest possible lifecycle in conveyors, and allow cost, time and safety benefits.
New Tivar HPV is suitable for all touch points in a conveyor system where friction and wear appears, such as chain guides, sliding strips and guides, rollers, single and multiple corner wear bends, and straight guides. As a fully certified Food Contact compliant material, it enables system operators to build-up a production line in accordance with the latest Food Regulation requirements.
The superior sliding performance reduces friction of components against a mating partner. From a cost perspective, this reduces energy use as considerably less drive is required to push the system. It also better protects parts from wear, in particular expensive sliding partners such as chains and belts, leading to a reduction in the purchasing and installation of replacement parts.
Longer performance periods without maintenance improve the overall safety of the system for operators.
The sliding advantage generates smoother, quieter operation without the need for external lubricants such as oil and grease, protecting the environment and reducing noise pollution from the equipment.