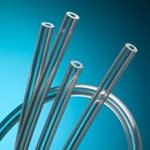
"PolyOne continues to address major healthcare trends toward improved patient safety and lower costs by providing innovative, versatile and regulatory-compliant materials," said Charles Page, global marketing director, PolyOne GLS Thermoplastic Elastomers. "Versaflex HC has excellent self-sealing performance and resistance to coring, addressing major drawbacks of traditional materials. We are currently working with key pharmaceutical OEMs in applications that leverage the multiple advantages of this material."
By replacing traditional stopper and septum materials with insert-molded Versaflex HC, PolyOne healthcare customers can achieve:
- Excellent self-sealing: Formulated specifically for resealing applications, Versaflex HC avoids coring contamination that is characteristic of traditional vulcanized rubber, which can leave particles of material behind during needle insertion.
- Resistance to coring: Testing Versaflex HC for resealing and coring performance with needles as large as 16 gauge achieved excellent results including good resealing after multiple penetrations.
- Enhanced purity: Because it does not use sulfur, zinc or other cross-linking agents common in curing vulcanized rubber, Versaflex HC reduces the risk of leaching and the resulting interactions with sensitive pharmaceuticals.
- Reduced manufacturing cost: Versaflex HC processes in a simple, one-step injection molding operation vs. the multiple steps needed for vulcanized rubber. In addition, these materials do not need the washing step required with conventional rubber.
- Streamlined regulatory compliance: This material meets the requirements of the ISO 15759 standard for medical infusion equipment, and can be steam autoclaved using temperatures up to 126C.