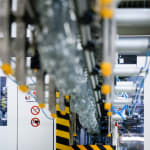
The district of Knetzgau in Lower Franconia is home to a good 6,400 people. Not far from the idyllic center of this little town on the River Main stands one of the biggest Coca-Cola factories in Germany. Here, Coca-Cola Europacific Partners (CCEP) employs around 500 personnel, producing its popular classics Coca-Cola, Coca-Cola Light, Coca-Cola Zero, Fanta, Mezzo Mix, Sprite and various others on a site measuring 200,000 square meters.
The group has made it its aim to create a more sustainable future and has adopted a holistic approach to this end. Saving energy, water and materials is beneficial to the environment and at the same time cuts costs. The production plant in Bavaria has now taken a further step in this direction by investing in the resource-conserving InnoPET Blomax from KHS.
Near infrared and Double Gate considerably reduce energy consumption
The latest generation of KHS’ proven stretch blow molding machinery is not only distinguished by its high performance but also scores in direct market comparison with various measures designed to save energy. Two in particular stand out here: firstly, the heater used to heat the PET preforms operates with what’s known as near infrared radiation (NIR) that in itself is far more efficient than many of the infrared heaters otherwise installed. Secondly, the InnoPET Blomax conveys the preforms without primary reflectors in two lanes on both sides of the lamps, enabling their energy to be applied much more effectively for heating. In addition to its specific energy savings, the Double Gate is also more compact than standard preform heaters.
In Knetzgau, project manager Ralph Sauter spent a long time deliberating over the investment in advance, drawing up a comparison of various systems on the market. Not one but two old stretch blow molders manufactured in 1998 were to be replaced that were no longer expected to satisfy the company’s requirements regarding energy efficiency and the general availability of spare parts. A decision was ultimately made in KHS’ favor. “In view of the targets we’ve set ourselves, saving energy plays a big role for us. With its new Double Gate technology and the savings this makes, the KHS system was of great interest to us,” says Sauter. Now that the machine has been up and running for a few weeks since its successful acceptance, he reckons on saving up to 560,000 kWh per year. This is an impressive figure in the face of constantly rising energy prices. “All suppliers have understood the importance of this issue,” states Sauter, but “compared to other systems on the market, the KHS setup generates far greater savings.”
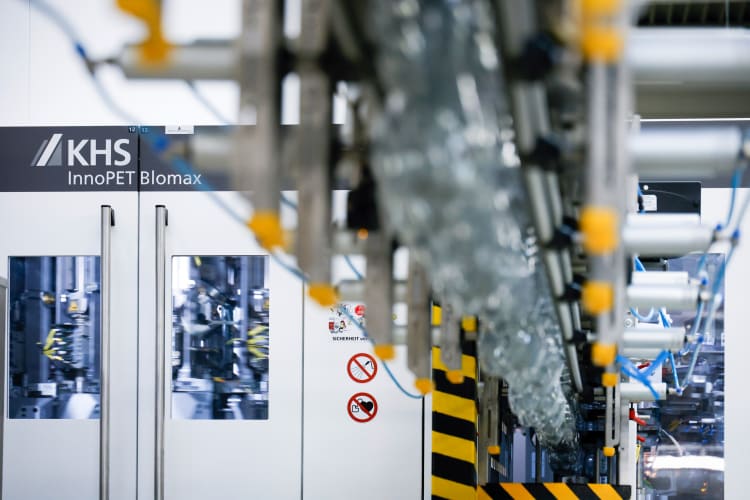
Design engineering challenges mastered
“We’re impressed by the functionality and performance of our new machine,” he adds. “The Blomax processes 20,000 2.0-liter containers and 30,000 1.5-liter containers an hour - and as it’s so flexible, it can be perfectly integrated into our line.”
The project manager also points out that the production site is not without its particularities. The biggest challenge was to convert the existing bottle air conveyor so that it served not two but just one machine. As the conveyor’s position was fixed, the new system had to be aligned in the bottle shop with centimeter accuracy. This is confirmed by Marc Harald Eysel, sales manager for PET Technology at KHS. “This was an exciting task for us.” He’s keen to stress, however, that adjustments like these in the interests of the customer are a matter of course for KHS. “We don’t just want to convince our clients with the system performance alone.”
While requirements in Knetzgau have initially been met by the new investment, KHS is generally seeing a fast-growing demand for energy-cutting technologies such as the Double Gate. “Even in comparison with modern stretch blow molding systems installed up to about the end of the last decade, our machinery saves a maximum of 30% in energy,” Eysel concludes.