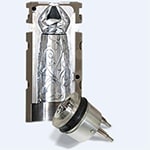
For blow molds to work well, regular greasing operations are needed: moving parts generate friction. Two minutes per operator and per mold are needed for these weekly maintenance operations. How can these operations be reduced? Simply by eliminating the greasing step.
This is how Sidel has innovated with Kohlox, a thermo composite material with a low coefficient of friction, helping parts move freely without any lubrication. Developed after two years of R&D, this material is the best compromise between mechanical resistance to impacts and compression, while also ensuring free movement of parts. Two new grease-free parts have been produced for the molds: wear rings for the mold bottoms, and female studs. In 2009, these new parts have been tested and validated on the industrial scale in partnership with Nestlé Waters Est France.
As a self-lubricating material, Kohlox offers significant savings in mold maintenance time, while also eliminating the use of consumables for those operations. Reducing maintenance time means improving blow molder availability and therefore productivity.
Régis Leclerc, technical coordinator for Nestlé Waters, explains: - One of our concerns is to reduce the time spent on mold maintenance and greasing. Any solution that reduces those maintenance steps helps significantly improve machine availability. We have saved about one hour of maintenance time on an SBO 20 thanks to the new molds with Kohlox parts. This significant time gain allows us to produce more or to perform other maintenance operations. That’s quite considerable if this technology is extended to all of Nestlé Waters’ blow molders running at full capacity.”
This self-lubricating material also helps improve mold cleanliness by eliminating the possibility of grease splashes or deposits, which are sources of persistent dirt. Régis Leclerc stresses the importance of this aspect: - Mold maintenance requires good training for operators, so that they can apply just the right amount of grease to keep the bottles clean and ensure good production hygiene. By eliminating the greasing step, we avoid the risk of non-quality problems associated with handling the molds and the other essential blow molder components.
Finally, the low density of Kohlox, which is four times lighter than steel, helps lighten the mold base to accommodate new blow molder speeds of 2,000 bottles per hour per mold, and reduces mechanical wear on the machine itself.
Patented by Sidel, this technology is available as an option for most new molds and can also be adapted to several existing molds for all types of Sidel blow molders. The verdict at Nestlé Waters is positive: - This project has been successfully completed thanks to an excellent collaboration with Sidel, whose staff has been present at our site to monitor the performance of the Kohlox parts. Because of the excellent results with the new molds, we have decided to order nearly 100 more molds equipped with Kohlox parts and also to adapt some existing molds.