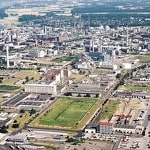
Specialty chemicals company LANXESS has completed the expansion of its Baypren polychloroprene solid rubber production operations in Dormagen. Werner Breuers, member of the LANXESS AG Board of Management, and Jan Paul de Vries, head of LANXESS’ High Performance Elastomers business unit, officially inaugurated the new production line today, Wednesday. It uses the innovative dry finishing production technology developed, tested and taken to the market-ready stage by LANXESS specifically for this purpose. This technology enables Baypren to be manufactured in a more resource-friendly way. LANXESS is also adding two new variants of this high-performance synthetic rubber to its product portfolio at the Dormagen site. The specialty chemicals company has invested some EUR 18 million in expanding production.
“This investment is further proof of our leading know-how in the field of high-performance synthetic rubber,” says Breuers. “By expanding our Baypren plant, we are providing the market with new impetus and demonstrating our strength to our customers. The new production line also once again highlights our staff’s impressive innovative skills and inventive spirit,” he adds.
Innovative production technology
The innovative dry finishing technology now being used at the Baypren facility in Dormagen reduces the number of production steps and conserves resources when manufacturing the synthetic rubber, among other things by dehydrating the rubber in a special extrusion device. This means far less water is required, which also reduces the amount of wastewater generated. The natural gas previously needed to dry the rubber is no longer necessary either, so less waste air is produced.
As a result of the production expansion, LANXESS is also offering its customers two new Baypren grades under the names “Baypren High Performance” and “Baypren Green Finishing.” Both variants are manufactured on the dry finishing production line. “Our new ‘Baypren Green Finishing’ grades feature enhanced crosslinking, while ‘Baypren High Performance’ benefits from further optimized flow behavior. These properties help increase the speed of the injection molding process for technical moldings and reduce energy consumption,” explains de Vries. “This results in significant economic benefits for our customers,” he adds.
The existing production lines will remain in operation to meet the continuing customer demand for “traditional” Baypren grades. By expanding the plant, LANXESS is increasing its annual production capacity in Dormagen by some 10 percent to a total of 63,000 metric tons of solid rubber.
Baypren high-performance rubber – highly versatile
Baypren high-performance rubber grades are highly versatile and combine good resistance to weathering, oil and heat with impressive impermeability to gases. Applications include the automotive sector, where they are used to make windshield wipers, hoses, belts, seals, insulating foams and air springs. They also help ensure that no air escapes from the floats of dinghies and protect against hypothermia and injuries in watersports suits. Globally speaking, this LANXESS material is used to make nearly one in two protective suits of this kind.
Dormagen – center for high-performance synthetic rubber
With a workforce of around 1,000, Dormagen is the third largest LANXESS production site in Germany and one of the most important sites for synthetic rubber worldwide. The Baypren facility alone, which belongs to LANXESS’ High Performance Elastomers (HPE) business unit, employs some 250 staff. HPE is part of LANXESS’ Performance Polymers segment, which recorded sales of EUR 4.5 billion in fiscal 2013.