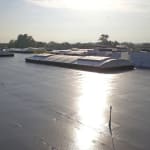
In the construction sector, because EPDM sealing films especially need to deliver excellent protection against leakage over the lifetime of a building, new mixtures represent a constant challenge to suppliers. In order to developed EPDM films further, Maag is unveiling a gear pump as a laboratory solution. This will enable the end product - film - to be optimised to a laboratory scale and “tuned” for new large-series applications.
Although penthouses with sloping walls have their charms, the Mediterranean flat-roofed construction has become more and more commonplace in Central Europe too since the 1970s. Although flat roofs were quite striking to begin with, since they couldn't cope with the weather conditions prevalent in the region, they have been improved massively since then and, thanks to a plastic, are now given an almost "endless life".
This plastic is EPDM (Ethylene Propylene Diene Monomer), a terpolymer elastomer such like rubber that belongs to the family of co-polymers (as defined by DIN 7864). EPDM is manufactured from the byproducts of oil refinery ethylene and propylene.
Sealing webs have been extruded from EPDM for the construction sector since 1960. These sealing webs are primarily used to seal flat roofs, back-ventilated facades and ponds. The advantages of EPDM are clear. Sealing webs made from EPDM can stretch by up to 500% and are permanently elastic, even in extreme temperature fluctuations between -40°C to +120°C. A lifespan of decades makes these films the ideal sealing solution.
In light of the undisputable advantages in terms of durability (see table 1) offered by the saturated polymer framework, the realm of possible practical applications is extremely diverse. The Deutsche Industrienorm organisation talks about the M Group – the opposite of which is the R Group, to which monomers with unsaturated hydrocarbon chains such as natural rubber (NR) or styrene-butadiene rubber (SBR) belong – with limited possibilities.
Classic applications for EPDM films include: roof and construction seals, seals such as O-rings, sliding ring seals and flat seals, hoses for hot water and steam applications, absorbent mats for improved thermal insulation, pond liners.
Conventional EPDM rubbers have an ethylene content of between 45 and 75 weight per cent. Polymers with a low ethylene content (45 - 55 weight per cent) are amorphous and have the best flexibility in cold conditions. As the ethylene content increases, so does the crystallinity. Pure, linear polyethylene, therefore, is highly crystalline. An EPDM with a moderate ethylene content (55 - 65 weight per cent) is partially crystalline.