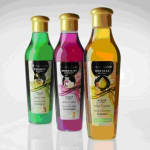
Natural cosmetics company Bielenda, in Krakow, has just begun marketing a new range of bath oils labelled Afrodyzjak, Ekstaza and Euroforia. They will be sold in various European countries, as well as on other continents. Bielenda wanted to pack the products, intended to stimulate the senses, in bottles that showed off their colours and transparency to best advantage, and which were in keeping with the very high quality image it was trying to promote.
After considering various processing technologies and alternative materials, including PVC and PETG, Bielenda picked extrusion-blow moulded bottles made from an ultra-clear polypropylene containing Milliken’s high performance clarifier Millad NX8000.
The polymer, with its low density and high mechanical properties, lets Bielenda minimize materials usage: polypropylene bottles can weigh around 20 percent less than PVC versions and as much as ten percent less than PETG bottles. Additionally, it is fairly easy to process (no need for pre-drying) and there are no issues with equipment corrosion. Extrusion blow moulding is a highly cost-effective process and allows for great freedom of design.
"The level of transparency provided by Millad NX8000 helps our products successfully stand out from others on the shop shelf,” says Bielenda’s marketing manager Magdalena Koćwin. “We invest significant resources in developing natural cosmetics and the packaging should emphasise the message. We expect this combination of an excellent product in an outstanding package to be particularly attractive to consumers looking for something a little bit special.”
Although blow moulding only accounts for a small fraction of all polypropylene consumption, PP does have a significant share in the plastics packaging market overall, and is second behind HDPE in the extrusion blow moulding market.
“Milliken’s Millad 3988 clarifying agent for polypropylene has been the industry standard since the early 90’s,” says Bernard Vermeersch, Senior Development Engineer at Milliken. “Millad NX8000 takes clarification to the next level, and that is obvious when you look at what it achieves in injection moulded and injection-blow moulded containers.” Its typical 50 percent reduction in haze versus the current industry standard makes highly transparent polypropylene a reality, even in relatively thick wall sections.
But until very recently the benefit has been more difficult to see in EBM containers than in other types of containers, because clarity depends to a certain extent on wall surface. Normally, the low pressures and the mould surface finish used in EBM don’t yield the best wall surfaces.
“Now, latest resin designs help combat this problem,” notes Vermeersch. “New grades containing Millad NX8000 can yield EBM bottles with opticals on a par with PVC. Processors can achieve gloss levels of 120 at an angle of 60 degrees, clarity levels of 95% and haze as low as 6%. These values have never been achieved before with PP in EBM.
For relatively low volumes, Extrusion blow moulding with Millad NX8000 clarified PP is much more cost efficient than injection-stretch-blow moulding with PET.
Milliken expects many more applications for Millad NX8000 in extrusion-blow moulded PP containers in the coming months.