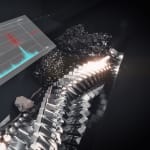
Vecoplan is continually developing solutions to make shredding processes more efficient. This can be seen in a number of innovative technical features. Most important, the company is placing increasing emphasis on digitalisation. Data can be used for reliable monitoring of processes and automation of work steps. This helps operators to avoid errors that arise when shredders are set manually. It boosts the performance of the machines and extends their service lives.
“Many machine parameters that workers formerly set manually can now be managed automatically,” says Paul Mockenhaupt, who is responsible for digitalisation at Vecoplan. “For us it’s becoming more and more important to equip our machines with intelligence so that customers have better support.” With this in mind, Mockenhaupt and his team are developing technical features to improve shredding processes. One example is an electrically powered ram.
Electrical means energy-efficient
“We’ve equipped our new electrically powered ram with highlydynamic ball screw drives,” explains Vecoplan’s developer. “Thanks to the high efficiency of these components, users benefit from excellent energy savings.” An electrical system, in contrast to a hydraulic one, does not need oil that can contaminate the output material. This is becoming more and more important to customers. Another key aspect is robust design. An electrical drive requires fewer mechanical parts, and that means less wear.
“Also, as compared to a hydraulic ram, our new solution can be better controlled. Users can set the torque, and thus the pressure applied to the material, very exactly,” says Mockenhaupt. The electrical ram steadily moves the input towards the rotor on the shaft. The new variant is also more dynamic and thus faster, which raises the throughput.
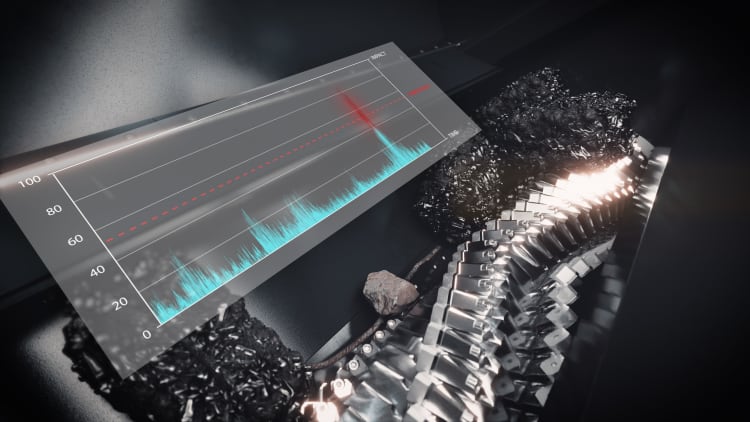
Powerful direct drive
Vecoplan can optionally equip its shredders with its more powerful and efficient HiTorc direct drive, which operates economically even at higher throughputs. “A controller integrated in the frequency converter ensures that the optimum torque is available at the rotor shaft at all times and in all operating conditions,” says Mockenhaupt. As a result, the drive is extremely energy-efficient. What is more, this purely electrical solution requires no clutches, belt drives or flywheels, which means that maintenance costs are much lower. “And because mechanical components are eliminated, the mass moments of inertia in the entire drive system are also significantly reduced,” adds Mockenhaupt. “The high availability of the torque enables a problem-free start-up under load, i.e., when the shredding area is full.”
The fully automated control system uses continuous speed analysis and electrical current evaluation to detect machine overload at an early stage in the ongoing shredding process. If extraneous material is encountered, the rotor shaft will stop in just a few milliseconds, preventing damage to important components. After a short counter-rotation, the Vecoplan drive turns in the required direction again in a few seconds. The synchronous motor also has a truly impressive degree of efficiency. Compared to shredders with electromechanical drives, shredders that are equipped like this can save up to 40 per cent energy - and even up to 60 per cent compared to hydraulic drives.