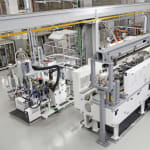
All in one: ColorForm complete system
With around 7,000 employees, Rehau Automotive is a well-known Tier 1 supplier of automotive exterior components worldwide.The company produces a broad portfolio of plastic components such as bumpers, spoilers and ventilation systems - often including surface finishing in a wet painting process. Thanks to the strategic investment in a complete ColorForm system (MX 2300 SpinForm with spin platen, automation plus RimStar-Compact 8/8 ColorForm) plus several tools, Rehau Automotive in Feuchtwangen is now a technological trendsetter. Axel Oberkampf (Head of Manufacturing Engineering at Rehau Automotive) describes the goal: "By combining in mold labelling, injection compression molding and PUR painting, we want to industrialize an innovative product and process concept for future series development - and encourage our customers to lead the way.The well-timed multi-component injection molding process is like a well tuned symphony orchestra, as numerous components and processes have to work together precisely in timeFront panel of the future
First, a decoratively printed IML film is automatically cleaned and transferred to the first mold cavity by a robot. This is then processed in several steps to create a front panel with a high-quality look, which is finally coated with a self-healing IMC polyurethane protective layer in the mold. Johann Reichstein (Project Engineer Advanced Development at Rehau Automotive) describes the trick: "The individual process steps are combined and parallelized in the tool in such a way that we combine three materials and the film insert into a completely finished product before the product leaves the injection molding cell. This means that no subsequent painting steps are necessary." The new front panel from Rehau, measuring around 600 by 1200 millimetres, is finished. The panel can be optionally extended with innovative lighting functions. Rehau Automotive is cooperating with ZKW to integrate the lighting technology.
Intelligent machine control
The entire process is integrated into the MC6 machine control system - even with a few special features. An automated process allows the sequence with and without PUR painting, and if a pre-molded part is detected as “Not OK” by the system, it is ejected and also no longer covered with the PUR layer. The process is determined on the basis of the data collected, which is provided to the customer in high resolution by KraussMaffei’s dataXplorer. The dataXplorer documents up to 520 machine signals from the injection molding machine and dosing system with a resolution of up to five milliseconds and saves them in curve sequences. This allows the user to view the entire process as if under a microscope. A file is created for each cycle, ensuring complete traceability.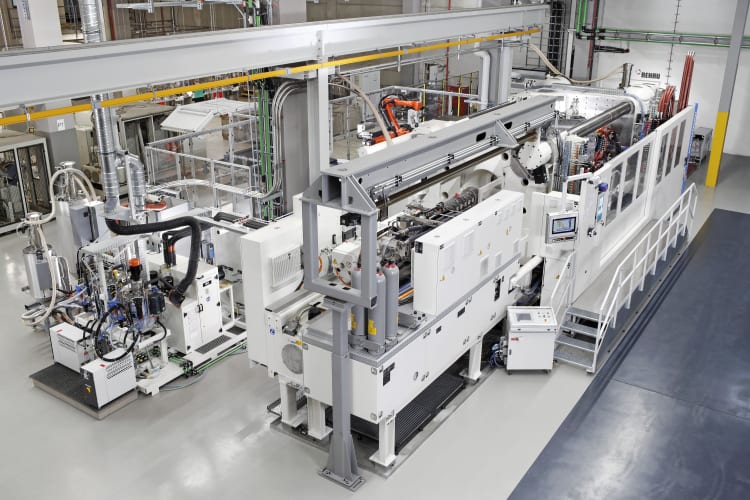
Injection molding and reaction technology from a single source
For PUR painting, an MX 2300 SpinForm with spin platen and 23,000 kN clamping force, a RimStar Compact 8/8 ColorForm metering system and automation work together perfectly. KraussMaffei is the only supplier in the industry to have both injection molding and reaction process machinery expertise in-house. Frank Burkhardt (responsible Area Sales Manager IMM) knows the advantages: "This means that interfaces are perfectly coordinated. For many customers, the fact that they receive the entire production cell from a single source is a decisive factor in their investment."This is also helpful when - as with Rehau Automotive in Feuchtwangen - the space conditions are somewhat difficult due to building heights and existing expansion joints. The project team initially started planning with the RimStar Flex dispensing machine, which is particularly versatile. After several layout optimizations, a RimStar Compact was the solution - this was very attractive in terms of price, but of course only works if several models are available.Long-term partnership
Rehau Automotive and KraussMaffei have a long-standing partnership and both companies are also celebrating anniversaries. The Rehau Group is celebrating its 75th anniversary this year, while KraussMaffei can look back on 186 years of history. The acceptance of the ColorForm system at the technical center in Parsdorf was a celebration of over 260 years of industrial expertise. As a visible sign of the collaboration, KraussMaffei presented the guests from Rehau Automotive with the Group's 75th anniversary logo - produced using its own powerPrint 3D printer.
Electromobility is only at the beginning of its development and with it the redesign of the familiar radiator grille. Rehau Automotive and KraussMaffe show where the journey can take us with their demonstrator involving injection molding and PUR painting. You can see it live at the KraussMaffei booth at Fakuma (October 15 - 19, Hall A7, Booth 7303).