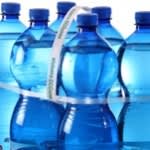
Shrink-film, however, requires fossil raw materials for its manufacture, and in the shrink-on process in the shrink tunnel, moreover, energy consumption is relatively high.
The goal of the development work at Krones AG was accordingly to create a resource-economical alternative to film-wrapped shrink-packs, a complete pack system including the packaging as such and the associated machinery. Krones was able to tap into strapping technology already trialled and used with success in other sectors, thus creating a completely new packaging design for PET containers, called Krones LitePac.
Users will also benefit from cost economies compared to shrink-films, with some estimates exceeding 50 per cent. This entirely new packaging design addresses market trends for secondary packaging of PET containers – not least in regard to eco-compatibility, resource-economy, reduced energy consumption and cost savings – and signposts a pack concept of the future.
The requisite technology is provided by the newly developed Evolite packer, comprising a container infeed module and a container strapping module. In the infeed module, the containers are divided into two continuous lane flows. Four strapping units then create the LitePac packs in the container strapping module.
Summa summarum, quite dramatic cost savings are anticipated thanks to lower packaging material costs, plus substantially downsized energy consumption, now that the shrink tunnel and an additonal handle applicator have been eliminated. This corresponds to a cost reduction of more than 50 per cent compared to shrink-films as a packaging material.
Fewer conveyors, reduced footprint, a simpler line layout, a smaller storage area in both the warehouse and the supermarket, less pallet traffic – all this does its bit to make the pack strapping technology a truly up-to-the-future concept.