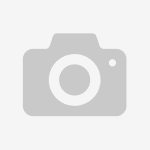
Bormod BJ368MO was selected by Piber Group for its exceptional and unique combination of very high flow and high strength, high impact resistance that is retained at temperatures as low as -20°C and the low odour and taste characteristics that are essential for food packaging materials.
Bormod BJ368MO is a ground-breaking polypropylene (PP) block copolymer that allows the injection moulding of tubs at higher rates and more cost-effectively than ever before. Tubs can be readily hot-filled.
Borealis developed high flow, high impact and high strength Bormod BJ368MO specifically for food-contact applications such as margarine tubs, containers for fresh and frozen dairy products and salads, as well as housewares. The grade makes use of Borealis` highly innovative Borealis Nucleation Technology (BNT), which increases productivity through faster and finer crystallization. It incorporates anti-static additives, not only to improve the cleanliness of finished products, but also to reduce cycle times by ensuring smooth demoulding, even at temperatures as high as 90°C.
Piber`s technical manager Paolo Bergaglio is particularly happy that his company upgraded to the new material. - Our food industry customers are increasingly demanding lighter weight packaging solutions, but with ever stricter criteria for drop and stacking performance, high quality and good aesthetics - he comments.
The material, the result of intensive research at Borealis into new and improved ways to add value along the value chain, has a melt flow ratio (MFR) of 70 g/10 min. This means that processors can easily produce parts with wall thicknesses as low as 0.4 mm, and fill moulds with flow paths having length: diameter ratios as high as 300:1.
This exceptional flow, coupled with ability of Bormod BJ368MO to crystallize rapidly and at higher temperatures than normal, yields significant cycle time reductions that can be as high as 20 percent. These processing improvements, together with the excellent end-use properties, translate into the potential to cut part weight by a similar amount.
Tubs made with Bormod BJ368MO have the impact resistance needed to minimize breaking problems on filling lines, in-store and in the kitchen, with good drop performance in refrigerator and deep-freeze conditions.
- As a leading provider of innovative, value creating plastics solutions for the packaging industry, we set out to continuously improve performance and drive improvements throughout the value chain - says Wim Roels, Borealis Vice President for Business Unit Moulding. - This particular grade, which we introduced at K2007, has proven to set a new standard in high flow, high impact polypropylene (PP) and provides a step-change in productivity.