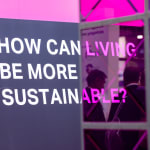
K 2025 from 8 to 15 October in Düsseldorf has set itself the goal of addressing the central issues of our times. One of its three Hot Topics reads “Shaping the Circular Economy”. Reason enough to shed some light on the current state of affairs in terms of circularity six months ahead of the world-leading trade fair of the plastics and rubber industry.
The world is experiencing a raw material crisis: more than 100 billion tons of raw materials are consumed annually but over 90% of the raw materials used are not recycled. An alarming ratio flagged up by the European Investment Bank (EIB). Rising CO₂ costs, volatile raw material prices and geopolitical insecurities put additional pressure on companies to manage resources more carefully.
Circularity is considered the decisive lever for achieving a sustainable future. An analysis by management consultancy Material Economics shows that Europe could save 450 million tons of CO₂ equivalents through closed material cycles by 2030 - this corresponds to 8% of the current emissions. In the long term, the Ellen MacArthur Foundation forecasts that up to 45% of emissions could be avoided by a closed-loop circular economy.
This transformation also holds enormous economic potential: according to estimates by consulting group EY, the use of secondary raw materials reduces energy consumption by 20% to 90%, saves large amounts of water and could save European firms up to EUR 465 billion in material costs per year. The International Labour Organisation (ILO) also expects seven to eight million new jobs to be created worldwide by the transition to a circular economy by 2030. More and more use cases show that circularity makes not only ecological but also economic sense. For instance, the German Cabka Group annually produces pallets and crates from some 150,000 tons of recycled plastics by their own accounts - proving thereby how waste can be turned into valuable products.
Plastics industry: a key sector with catching up to do
The plastics industry plays a pivotal role in this transformation. In 2023 413.8 million tons of plastics were produced worldwide, according to Plastics Europe, but the share of recycled materials continues to be low: only 8.7% of plastics were recycled - most of them by mechanical recycling - whereas the lion’s share was incinerated or landfilled. This is happening even though recyclates hold an enormous potential. Their production requires markedly less energy than the production of new products from fossil raw materials, thereby substantially reducing CO₂ emissions. On top of this, their use increases supply security - a factor of rising importance in times of geopolitical crises.
However, recycling is technically demanding - and often more expensive than producing new plastics. After all, post-consumer plastics have to be sorted, cleaned and prepared with great effort. In addition, the legal requirements are strict, high-quality recyclates scarce and many processes energy-intensive - all resulting in higher production costs compared to new plastics. “But nobody wants to pay higher costs,” stresses Ulrich Reifenhäuser, Chairman of the K Advisory Board. “Plastics are so successful because they are so much better than other materials. But the transition to the circular economy costs money. This cost issue will not be overcome without regulatory requirements.”
However, the responses to the question of how the transition to a functioning circular economy will work vary from country to country.
Europe looks to regulation
While other nations focus on voluntary commitments and market-oriented solutions, Europe regulates by law. Strategies such as the “Circular Economy Action Plan” (CEAP) and regulations such as the Packaging and Packaging Waste Regulation (PPWR) and the Single-Use Packaging Directive (SUPD) drive the transition to circularity by means of recycling rate, mandatory recyclate content and Extended Producer Responsibility (EPR). The PPWR shows how this works: since 2025 single-use PET bottles have to contain a minimum of 25% recycled plastic and this percentage will go up 30% by 2030. For manufacturers such as Coca-Cola or Nestlé this means rebuilding their supply chains, sourcing high-quality recyclates, adapting production - otherwise they run the risk of a sales ban. The SUPD is also having an impact: in Lithuania the return rate of PET bottles shot up from 34% to 92% after the introduction of a deposit system - in as little as two years. Companies face major challenges in the process: the limited availability of high-quality recyclates, the technical complexity of changing over to a recycling-friendly design - not forgetting the short deadlines set for complying with these often complex requirements.
Chemical ingredients are also increasingly moving into the focus of the EU. Especially disputed is the handling of PFAS since a ban could make recycling considerably more difficult - because plenty of waste plastics would then be classified as contaminated and eliminated from the circular economy. Wolfgang Große Entrup, Director General of VCI, therefore warns against a blanket ban: “With each individual substance banned in the EU the risk grows that more of our industry players move to less regulated regions. This, however, does not solve the original problem.”
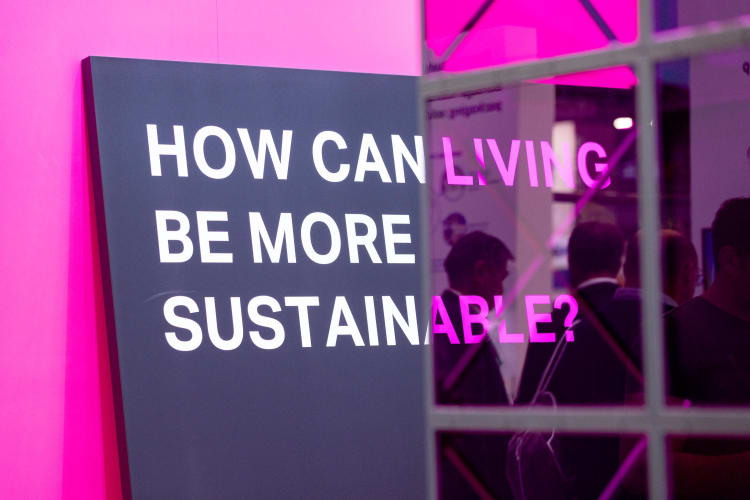
Asia: between advances and structural deficits
Accounting for 53% of global plastics production Asia is the main player - and the main source of plastic waste. While some countries pursue ambitious recycling strategies, others lack the basic infrastructure.
China’s circularity offensive: centrally controlled, consistently implemented
For a long time, China was the biggest importer of plastic waste, now the country is recharting its course. By adopting its “National Sword Policy” the country has stopped the imports of unsorted plastic waste and is now driving the expansion of own recycling structures. The 14th 5-year plan focuses on modern collection and sorting systems and promotes both mechanical and chemical recycling. By 2035 the industry aims to be largely decarbonised and have transited to closed material cycles. This strategy is accompanied by the “Circular Economy Promotion Law”, which obliges companies to take back and safely dispose of specific products, and the establishment of the state-owned “China Resources Recycling Group” with the aim of centrally controlling the transformation.
Japan and South Korea: driving technology systematically
Japan and South Korea are among the pioneers in circular economy - not least due to clear political objectives and early-adopted legislation. In Japan the “Container and Packaging Recycling Act” has already obliged companies since the 1990s to participate in return and recycling systems. This is supported by the “Plastic Resource Circulation Act” adopted in 2022, which promotes recyclate use and prescribes detailed recycling plans for plastic products.