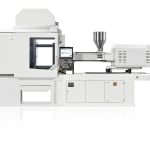
Efficiency in the medical sector is reliant on equal measures of precision and mass-production. It lays the foundation for reducing healthcare costs for patients and medical providers. At Fakuma 2024, Sumitomo (SHI) Demag will showcase how scalable solutions can be implemented to optimise productivity while simultaneously lowering the manufacturing cost per unit.
Conventionally, higher injection moulding shot weights require a larger machine. However, in another world first, the medical team at Fakuma 2024, now led by Business Development Director Medical Andreas Montag, will introduce an alternative, more compact 180 ton IntElect machine, powered by a new injection unit.
With the introduction of a 910 injection unit - the largest that can be accommodated in this 180 ton machine - the range of applications in the clamping force range of 130-180t is expanded. One of the key benefits of being able to select a smaller footprint machine that can handle larger shot weights are the rapid energy savings.
To demonstrate this flexible combination and fine processing control, on the main booth exhibit, an IntElect machine will mould syringe plungers with a shot weight of 29 grams, from a non-porous High-Density Polyethylene (HDPE) every 6,5 seconds, using a 32-cavity tool. This specific showcase is realised in cooperation with elm-plastic, who also supply the tool, cooling system and additional peripherals.
“This highly efficient yet compact cleanroom medical production cell is characterised by its repeatability and cleanliness. Built for high speed and precision, it is designed to handle extremely narrow tolerance medical applications produced in high volumes in the most efficient way, yet give processors the flexibility to mould everything from small medical parts to larger components,” expands Andreas Montag.
The ability to add a 50 mm screw allows processors to mould larger parts. Having the option to rapidly switch between three screw s (45, 50, and 60 mm, with the option to add 55 mm too), ensures that the optimum screw is selected to suit each medical application. Further increasing processing flexibility and production capacity.
Rather than automating the removal of components, this exhibit instead utilises a QA switch installed within the production cell. When the mould opens, the syringe plungers cascade onto the conveyor belt where rejected parts are segregated and the good parts weighed and counted into a changeable boxing system supplied by AM Plastics. “All of this is achieved without sacrificing any floorspace - productivity is increased by using floor and vertical space more efficiently, increasing output volume per square metre,” highlights Andreas Montag.
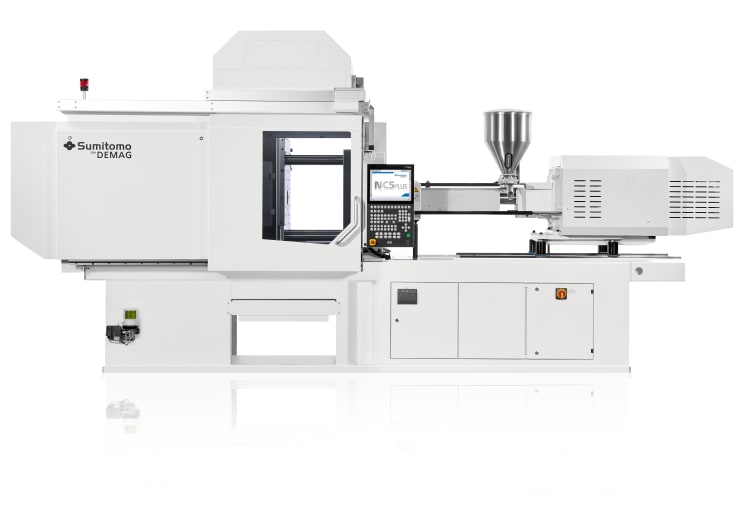
Scalable medical solutions
As specialists in medical processing, Hekuma on booth A7-7202 will present one of its scalable and flexible cleanroom configurations designed for petri dish production. Integral to this medical package is the IntElect2 100 system. Hekuma describes this year’s presentation an excellent example of a well-considered, automated, scalable turnkey system. Making it ideal for smaller production runs as well as delivering more value to mass manufacturers of medical components.
Drawing upon the complementary strengths of Asian tooling specialist Jestar Mold Tech, the Hekuma collaboration also demonstrates how high-end and innovative solutions can work together and be cost efficient. Rather than using a conventional stack mould to manufacture petri dishes, Jestar supplies the 2+2 single face tool to support a seven second cycle time and high production output. Hekuma provides the automation itself: a 6-axis robot removes the parts by side removal.
However, cost efficiency doesn’t mean compromising on standards. To maintain compliance with the explicit quality management and validation ISO 13485 standards for medical devices, the IntElect machine comes with set user parameters. This helps to ensure that processes are kept within certain bandwidths and that users do not make adjustments to pressure, temperature, flow and cooling settings without permission.
Each of the eight Sumitomo (SHI) Demag exhibits at Fakuma 2024 exemplifies the close collaborative approach that the company adopts with all industry partners, and the united drive to boost efficiency for processors locally and globally.