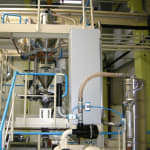
For reasons of cost effectiveness and to maintain flexibility during product changes, individually prepared manufacturing compounds are generally never or hardly ever used during nonwoven fabric manufacture. RKW Gronau always mixes the corresponding additive into the base material – matched to the use in the product – inline during the process. The Somos Gramix S9 series gravimetric dosing and mixing system put into operation there at the end of 2008 in the new nonwoven fabric plant is designed for a total of six formula components and a total material throughput rate of 1,000 kg/h.
As RKW Gronau also apportions functional additives such as UV stabilisers and flame retardants as a master batch in small concentrations, the decision fell in favour of gravimetric dosing. Purely in terms of costs, volumetric dosing, although cheaper, would have increased the risk that possible fluctuations in the bulk weight due to irregularities in the grain size distribution in the additive would also be reflected in temporal-local attribute fluctuations in the manufactured fleece.
Specialised in manufacturing synthetic nonwoven fabrics, the Gronau site, part of RKW SE, Frankenthal, is manufacturing mostly nonwovens based on polypropylene (PP). At present there are three lines producing with a total capacity of 12,500 tons per year. With the latest plant addition in 2008, RKW Gronau can now choose between two technologies for compacting the produced random orientation fleece after the spinneret: thermobonding (spunbonding), just as in the present nonwoven fabric plants, and now also the newer water jet compacting (spunlace method).