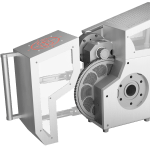
The main product that was presented at this year’s K fair is a rotary screen changer for the plastics industry. Continuity of the process, invariability of parameters, and easeof use are just three of its many advantages. Rotary screen changers represent the long provide version of screen changers for constant pressure processes in
the world.
The principle of operation of the rotary filter is based on a rotating disk, which is mounted between two filter blocks. On the screen disk - looking from the inlet block the side, there are special cavities - slots in which filter screens are placed. Witheach movement of the screen disc, a new screen is partially inserted into the melt channel, while at the same time the same part of the old contaminated screen is taken out. As a result of such a solution, the filtration surface area is constant, which ensures that the melt flow pressure is kept constant. This entails the invariability of the parameters of the molten material, which could lead to a change in its materials behavior (e.g. an increase in melt temperature of the material in the case of an increase in pressure during the processing of PVC, which has a negative impact on the quality of the final product). Such solutions prevent pressure peaks, and thus reduce extruder pulsations, and, above all, clean the processed material of any impurities. The cleaned material directly affects the better quality of the final product and the maintenance of production continuity, for example, foil, where the blow-up balloon breakage causes material and production losses, but also extends the delivery time. Rotary screen changers are very widely used not only in recycling processes, but also in the production of pure plastics (ABS, PE, PET, PVC, PP, PS, etc.) and a finished product in the form of foil, profiles, etc.
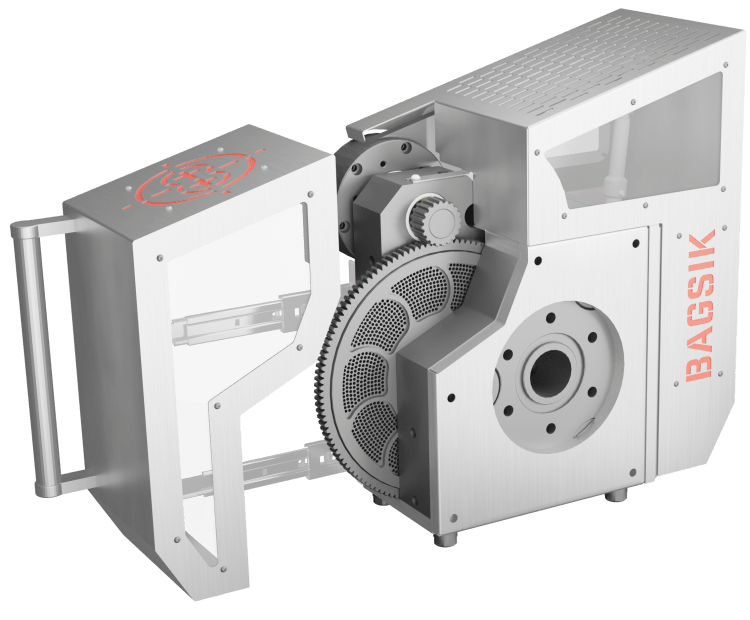
Rotary screen changers under the Bagsik logo successfully work within many production lines throughout Europe, with a maximum possible capacity of up to 5000 kg/h. The company produces automatic filter systems with and without self-cleaning system.
The self-cleaning version allows to reduce the number of workers and usage of the screens. Over the years, the self-cleaning system developed and improved in conjunction with dedicated automation, allows to generate cost and material savings.
Bagsik offer also includes:
- plate, bolts screen changers,
- complete lines for PVC processing,
- melt gear pumps,
- filter screens.
The company currently has 2 locations:
- Bagsik Sp. z o.o. in Gliwice,
- Bagsik Sp. z o.o. Sp. k. in a new location on 15,000 m2 in the special Economic Zone in Zabrze.