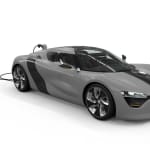
Radiation crosslinked plastics: High potential for electric cars - interview with Dr. Michal Daněk, Key Account Manager Radiation Crosslinking at BGS
How large is the market for radiation crosslinked plastics for automotive applications in Central Eastern Europe and how has this market developed in recent years?
The overall market for radiation crosslinked plastics in Central Eastern Europe is very difficult to estimate. The entire market is subject to constant change, particularly due to the current shift from conventional combustion engines to purely electrically powered vehicles. There are components made of radiation crosslinked plastics that are only available for the combustion engine and only generate functional added value for the overall vehicle concept here. The market for conventional vehicles has developed rather moderately in recent years. However, electromobility is providing new and strong growth impetus for the use of radiation crosslinked plastics.
What have been the main applications of radiation crosslinking in the automotive industry to date and what new or expanded fields of application do you expect to see as a result of e-mobility?
The current fields of application for radiation crosslinked plastics are in the area of the combustion engine and generally in applications that require increased temperature resistance, chemical resistance and, for example, creep resistance. Examples include exhaust pipes, bellows,
fastening elements and energy supply systems, i.e. cables. E-mobility is expanding the product portfolio on several levels. On one hand, the demand for cables, especially high-voltage cables, is increasing significantly. On the other hand, battery systems are opening up completely new fields of application. For example, the battery housing or plastic components in the battery itself. The critical load case "thermal runaway" can only be realized with temperature-resistant components. Radiation crosslinked plastics will play an increasingly important role here.
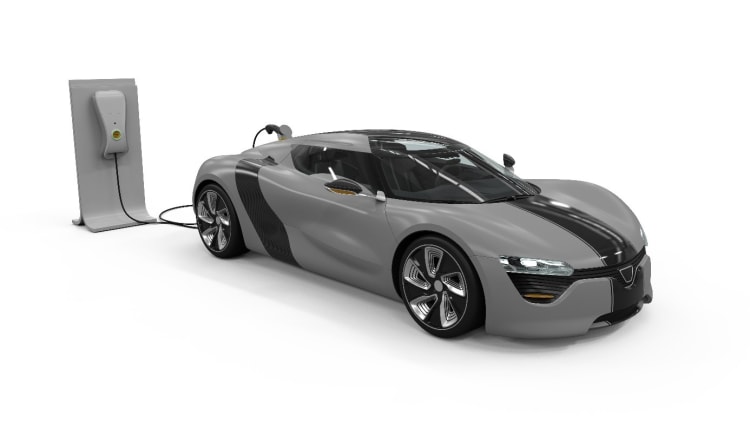
Source: BGS Beta-Gamma-Service
Which components or assemblies in the vehicle are suitable for radiation crosslinked plastics? Where can metal be replaced and where can high-strength plastics be replaced?
All components and assemblies with increased requirements for temperature and media resistance or impact protection are generally suitable for the use of radiation crosslinkable plastics. For example, in some vehicles, exterior components made of metal are replaced by radiation crosslinked PA66 with a 30 percent glass fibre content. Another example is fastening components such as nuts, screws and clips made from radiation crosslinkable PA66 instead of metal. The reason for this is the low density or lower weight and the better properties in terms of media resistance. An example for the substitution of high-performance thermoplastics or fibre-reinforced thermosets with radiation crosslinked thermoplastics can be found in the field of contactors.
How high are the cost savings in some typical applications compared to the materials previously used?
Cost savings can be achieved in several ways. Firstly through material substitution and secondly through our irradiation technology itself.
We always irradiate a "surface" on or in which the radiation crosslinkable plastic is located in the form of components. Let me give you an example: a 400x400x200 mm cardboard box can hold 1,000 radiation crosslinkable clips. The cost saving is achieved by dividing the irradiation costs for the box by the number of components in the box. This means that the irradiation costs per clip are very low. If the clips were previously also made of metal or fibre-reinforced plastic, a further reduction can be achieved by substituting the material with a radiation crosslinkable thermoplastic.
What role does BGS want to play in this development in the automotive sector and what are your growth plans?
E-mobility is one of the biggest growth markets of our time and we at BGS want to position ourselves accordingly. We are currently involved in various development projects and also in Start of Production (SOP). In addition, we are also looking into the possibilities of recycling radiation crosslinked plastics. We have already achieved very good results in this area, which we are incorporating into new projects. Another growth area is the irradiation of power semiconductors for applications in the fields of e-mobility and renewable energies. In other words, in many applications in which increasing electrification plays a role. We have been irradiating in series production for various customers at all three company sites for several years now.