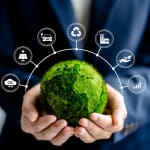
Complementing its Renycle range of engineering polyamides made from recycled nylon, at Fakuma 2024 (Hall A1 Stand 1106), RadiciGroup launches Bionside, a line of bio-based products comprising innovative engineering polymers obtained from renewable source raw materials. The new Bionside offering of bio-based grades is part of the Radilon family of products and includes both the products being sold under the Radilon® D (PA610) brand and the ones currently undergoing testing (PA56 - PA510 - PA1012). The choice of bio-sourced materials represents a strong commitment to reducing fossil fuel dependency, as well as product environmental impact and CO₂ emissions. Thanks to their chemical conformation, the polyamides made from renewable source materials feature high technical characteristics, which make them suitable for many applications.
In line with the Group sustainability strategy, RadiciGroup High Performance Polymers wants to make available genuinely innovative proposals that meet stringent technical requirements yet safeguard the environment and people, so as to meet the demand of its customers, who, in turn, are attentive to reducing the environmental impact of the value chain. RadiciGroup compounds are manufactured in state-of-the-art plants powered by renewable energy, are the result of significant R&D work and many years of experience in the market, produce no waste and, like all Group products, feature end-of-life recyclability. Moreover, the product environmental impact is calculated according to LCA methodology.
“We are stepping on the accelerator to deliver a product offering that guarantees high technical performance and, at the same time, ensures the sustainability of the projects developed together with our customers,” emphad Erico Spini, global marketing director of RadiciGroup High Performance Polymers. “At the fair, you can see several mass production applications achieved using our Radilon D (PA610). What’s more, we are taking the opportunity to introduce a few of our new experimental grades to our partners and discuss new paths to concrete sustainable solutions in our target application sectors through the use of a polyamide 610 with 64% renewable source content. According to our calculations, this new product will provide an estimated a reduction in CO2 emissions of close to 70% compared to a polyamide obtained from materials of fossil origin. The excellent results have definitely encouraged us to pursue the road ahead.”
Our PA610, obtained from castor oil plant seeds, is a product with very good hydrolysis and water contact resistance and, thus, ideal for many applications in the automotive sector, such as cooling line connectors, ducts, pump parts and thermostat housings, i.e., very high tech applications where safety plays a central role. Another industry where bio-based materials can make a difference – not only from an environmental point of view but also in terms of performance - is water management. On account of their excellent hydrolysis resistance, these materials have greater dimensional stability due to reduced water absorption, which is about 1/3 of the absorption of PA6 or PA66.
“Our R&D activities are focused on the study and testing of new products, including 100% bio-based materials and materials obtained from other renewable sources, with the aim of expanding our sustainable offering and enhancing specific technical performance,” Mr. Spini concluded.
At Fakuma 2024, the spotlight is also on a new family of PBT-based halogen-free flame retardant materials (Radiflam B), which expands the offering for the E/E and e-mobility sectors, giving customers an even more targeted and more sustainable choice for a large number of applications.
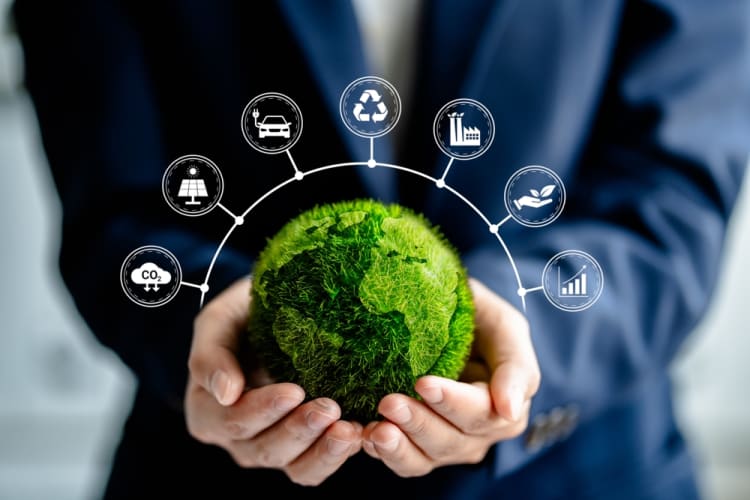
For the e-mobility sector, the Group is showcasing three new orange colour halogen-free products based on Radiflam B (PBT), Radiflam Aestus (PPA) and Radilon D (PA610 for extrusion). The expanded offering will provide for an even more specific choice when it comes to components operating under high electrical voltages: the operating conditions (such as the expected temperature) and also the technology used to manufacture the components will determine the most appropriate choice. In addition, the Radilon D solution allows for the use of a polymer partially obtained from renewable source material and, hence, with a lower environmental impact.
As regards cars, including those with endothermic engines, RadiciGroup is ready to deliver lower environmental impact solutions that can even be used in conventional applications. One example is an air intake manifold made of 100% Renycle, which won a Society of Plastics Engineers (SPE) award in June 2024: a high-tech application typical of the automotive sector, where the use of glass-fibre reinforced nylon has, over the years, almost completely replaced metals. However, in this case, the challenge was to use a 100% recycled material, the result of a careful process of sorting, cleaning and control of the raw materials to consistently ensure very high quality.
Finally, at Fakuma 2024, RadiciGroup is presenting some polyamide-based products for the hydrogen and fuel cell industries, where a very high growth rate is forecast in the coming years. In particular, a high-purity Radilon Aestus (PPA)-based material for fuel cell components is on display. As for the production of hydrogen tank liners, two materials from the Radilon S family (special PA6 for blow moulding and injection moulding) are showcased. The technical characteristics required for tank liners are high impact resistance at very low temperatures, low hydrogen permeability and easy processability.