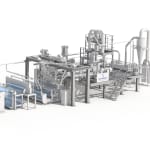
At Chinaplas 2025, the Reifenhäuser Group will present its latest technological innovations for the efficient and sustainable production of plastic films. The extrusion specialists will showcase at Shenzhen World Exhibition&Convention Center (Booth 10G21) from April 15 - 18 solutions that address the key challenges of today’s plastic industry: reducing resource consumption, increasing recyclability, and making production more autonomous and efficient. Meeting these demands requires advanced production technologies that Reifenhäuser already offers today.
A central focus at the show will be the use of Machine Direction Orientation (MDO) technologies for producing fully recyclable mono-material films with performance and cost-effectiveness equivalent to conventional multi material structures.
Marcel Perrevort, CSO of the Reifenhäuser Group, explains: “In the flexible packaging sector, we are currently seeing a huge trend away from conventional and non-recyclable mixed material laminates towards fully recyclable mono-material composites, both for blown and cast films. Our state-of-the-art MDO stretching units enable enhanced mechanical properties for all-PE or all-PP films. Thus, PET films commonly used in material composites can be replaced. By downgauging, we also reduce production costs to a competitive level, making recyclable films a profitable choice.”
It's all about MDO
With the EVO Ultra Stretch MDO unit for Reifenhäuser’s blown film lines manufacturers produce all-PE mono films for applications such as high barrier food pouches. Due to the stretch process film thicknesses of 18µm (with properties of a 25µm product) and less can be achieved, keeping production costs within the range of conventional films. With the patented integration of the MDO unit directly into the haul-off, the film is stretched in the ideal phase of the process - using the first heat - for maximum efficiency and film stability. Furthermore, the all-PE film achieves the required barrier effect with an EVOH content of less than five percent, fully meeting the criteria for recyclability. At the same time, Ultra Stretch enhances the performance of the EVOH barrier layer while reducing material usage, delivering cost and sustainability benefits.
The same applies to MDO technology in the flat film sector. With its CPP/CPE cast film line Reifenhäuser provides best transparency, printability, easy-tear properties, and sealing. The line features an MDO stretching unit that enhances the film properties, enabling recyclable all-PP mono films with barrier functions for food and medical packaging. Here too, stretching the EVOH layer improves the barrier effect while preserving recyclability. In addition, customers can opt for the unique Reifenhäuser automation system PAM (precise, autonomous, mechatronic) bringing cast lines to a whole new level. PAM automatically adjusts coextrusion adapters and dies via high precision actuators for optimum convenience, quality and productivity. Once recipes have been set, they can be saved and called up immediately at the touch of a button - even by inexperienced system operators. The high degree of automation makes producers independent of the shortage of skilled workers. Energy consumption is 99% lower compared to a thermal expansion bolt system, as the actuators only need to be supplied with power during the adjustment process and not permanently.
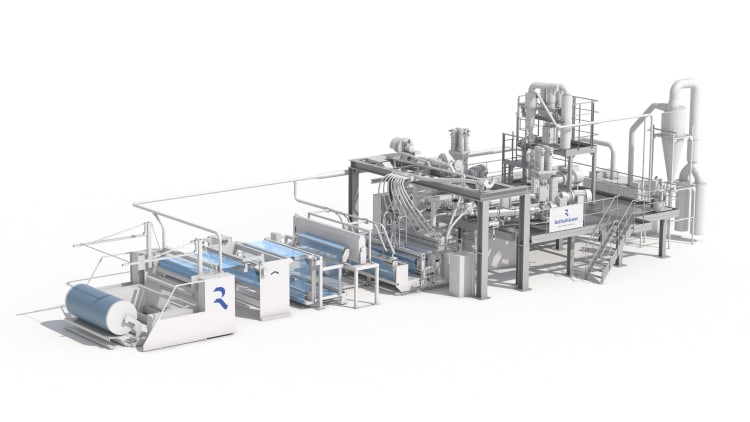
Kdesign: Market leading blown film cooling technologies
Kdesign, Reifenhäuser’s subsidiary and leading specialist in cooling, measuring, and calibration systems for blown film lines, will also be showcasing at the Reifenhäuser Chinaplas booth.
With the famous Karat cooling ring, Kdesign regularly sets benchmarks for maximum cooling performance, ultra-low film tolerances, and user-friendly operation. Processors all around the world rely on Kdesign solutions to improve blown film production in terms of quality and productivity. With an output capacity that is up to 50 percent higher than mid-range products and 25 percent higher than high-end competitors, the Karat cooling ring enables a significant increase in productivity, while at the same time maintaining excellent profile tolerances and top film quality.
In addition, Kdesign offers sophisticated secondary cooling units: With the Centro-Freeze, producers avoid film blocking in the haul-off by additionally cooling the bubble before it enters the flattening process. By using the Centro-Freeze, the output is therefore further increased, whiles producers save on anti-block additives and improve the film properties. All Kdesign components reflect over 20 years of experience in retrofitting existing blown film lines and equipping new OEM lines.