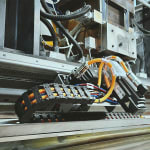
After extrusion machine specialist Reifenhäuser presented the automation system PAM (precise, autonomous, mechatronic) for flat dies and coextrusion adapters for the first time at the K 2022 plastics trade fair, the 150th system has now been installed on a customer line. The patented mechatronic control system has decisive advantages over conventional automatic thermal expansion bolt systems. PAM uses high-precision electric actuators to automatically control the adjusting screws for setting and regulating the flexible die lip. Depending on the die design, it is also possible to autonomously adjust the dust bar, the width adjustment and the lip opening by adjusting the lower die lip. PAM is available for all new Reifenhäuser flat dies and as a retrofit for dies from all third-party manufacturers.
The 150th unit was delivered to a customer in Germany who has automated his PET thermoforming sheet line with PAM. The system is characterized by its simple design and handling. At the same time, the sophisticated control works with absolute reliability and precision. In addition to the increase in efficiency, the system is now much easier, more convenient and safer to operate. Once settings have been saved, they can be called up via the system HMI and PAM delivers perfect and reproducible film quality at the touch of a button. Processors are therefore less dependent on the qualifications and experience of the system operators, achieve a faster start to film production, higher output and consume significantly less energy. This is because the motorized actuators only need to be supplied with power for a short time during adjustment and not permanently, like conventional thermal expansion bolts. The overall equipment efficiency (OEE) improves significantly overall.
Tim Bänsch, Product Manager at Reifenhäuser Extrusion Systems, explains: “With PAM automation, we can offer our customers a unique system that offers decisive competitive advantages thanks to the patented mechatronic control system and has proven itself in every respect with 150 systems on the market.”
The technology was developed by maku AG, which was founded by Robert Maeder in 1983. In 2022, Reifenhäuser Extrusion Systems (RES) - the Reifenhäuser Group's business unit specializing in extrusion components - entered into a strategic partnership with maku to jointly develop the PAM system further and market it worldwide. Reto Maeder, the current managing director, co-owner and son of the company founder, continues to be active in the development and customer support of the PAM system and is available with his many years of expertise in the field of mechatronic die control.
Simple operation and high work safety make producers less dependent on highly qualified personnel
Usually, starting up an extrusion line or changing products requires many skilled operations. Producers are therefore dependent on well-qualified machine operators, which is a huge problem in times of a shortage of skilled labour and high staff turnover. With PAM, producers become more independent, as the system itself can restore the optimum die setting at any time.
Another decisive advantage of PAM automation is the increased work safety. With a manually controlled flat film line, the machine operator works directly on the so-called hot part of the line. When using PAM, the operator does not have any contact with hot metal elements of the line or with the hot melt itself. Burns or other injuries caused by working on the running extrusion line are therefore ruled out. In this way, producers can easily fulfil the mandatory occupational safety requirements in high-tech markets, such as North America or Europe, and protect their employees in the best possible way.
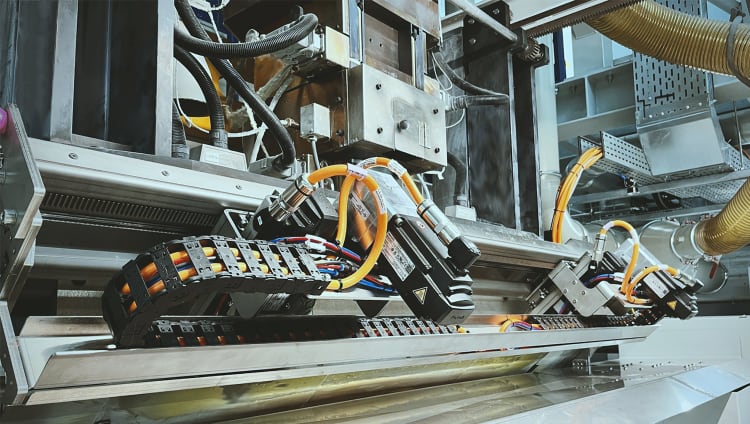
thermoforming sheet line.
PAM for coextrusion adapters
The PAM control system is not only available for flat dies but also for the Reifenhäuser Coextrusion Adaptor Pro. This feedblock is the only coextrusion system on the market that enables the profiling of individual film layers while the system is running. Unlike conventional solutions, the elements in the adapter do not have to be removed, processed and reinstalled in a time-consuming manner. Instead, profilers can be flexibly controlled individually or together during operation via a central adjustment.
With the PAM option, Reifenhäuser goes one step further and automates the setting of the layer distribution and simplifies adjustments and optimizations thanks to integrated recipe management. This is particularly worthwhile for manufacturers of films with many layers and many product changes.
While the coextrusion adapter for simple 3-layer laminates can be set in a few simple steps, up to 70 profilers need to be adjusted for barrier laminates with 11 layers, for example. Compared to manual adjustment by a machine operator, automation saves around half an hour of changeover time, depending on the number of profilers to be adjusted.
Reifenhäuser is one of the few machine manufacturers on the market that produces all hot part components itself - extruder, coextrusion adapter and die. Thanks to this hot part expertise within the group, all process-related interfaces can be perfectly designed to work together. PAM takes the whole package to a new level.