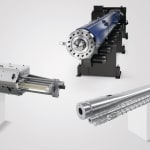
The Reifenhäuser Group, leading manufacturer of extrusion machinery and components, will be exhibiting at Fakuma in Friedrichshafen from October 17 to 21, 2023. Reifenhäuser will be represented at the international trade fair for industrial plastics processing in Hall A6 - Stand A6-6206 to showcase its latest blown and flat film technologies as well as components for extrusion and injection molding.
At Fakuma this year, the Reifenhäuser Group will focus on its broad competence network combined with a high vertical range of manufacture. Reifenhäuser manufactures all important core components in-house, which means that the customer always receives a perfectly coordinated overall system. For this purpose, the group of companies has highly specialized business units, three of which will be on site at the booth: Reifenhäuser Blown Film, Reifenhäuser Cast Sheet Coating and Reifenhäuser Extrusion Systems.
Reifenhäuser Extrusion Systems (RES) is the expert for melt-guiding and forming components. As a special highlight, RES will showcase its highly wear-resistant Reiloy screws and barrels at Fakuma, which regularly set benchmarks in terms of quality and performance. The components offer a demonstrably longer service life, thanks to precise matching of raw materials and additives. With the alloys developed exclusively in-house at Reifenhäuser and optimized for the process, processors of injection molding and extrusion products benefit from the best cost-benefit ratio in the industry. RES will also showcase its extruder and die portfolio as well as its multi-vendor upgrade and refurbishment program.
Ralf Pampus, Managing Director at Reifenhäuser Extrusion Systems, explains, "From the plasticizing unit to the die, we know all interfaces precisely and design them exactly according to customer requirements. We see ourselves as an independent partner and offer our components and services for both Reifenhäuser and third-party lines from all manufacturers."
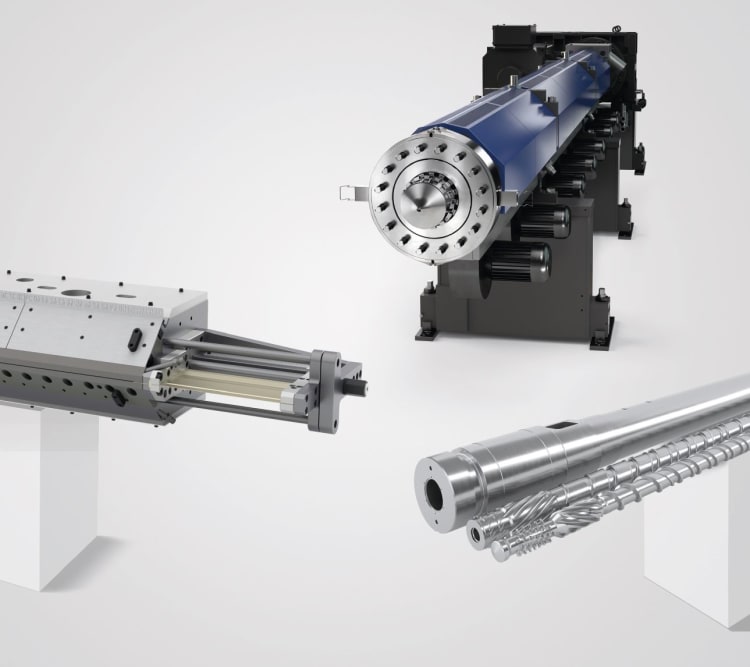
Reifenhäuser Cast Sheet Coating (CSC), as a supplier of complete flat film lines, will be exhibiting at Fakuma, among other things, its latest automation option PAM (precise, autonomous, mechatronic) for coextrusion adapters and dies. Using automated screwdrivers, PAM enables autonomous and mechatronic adjustment and control of the flexible lip conveniently via the line control system. Depending on the die design, autonomous adjustment of the dust bar, width adjustment and lip opening via adjustment of the lower die lip is also possible. In combination with the Reifenhäuser Coextrusion Adaptor Pro, PAM can also control the profiling of the individual layers while the line is running. This is significantly faster than conventional control by hand or thermal expansion bolts automation and enables faster start-up of good production, higher output and improved overall equipment efficiency (OEE). Once recipes have been set, they can be stored and recalled at the push of a button - even by inexperienced line operators, which is a decisive advantage against the background of the ongoing shortage of skilled workers. In addition, energy consumption is significantly reduced compared to an automatic thermal expansion bolt system, as the screwdrivers only need to be supplied with power during the adjustment process and not permanently.
Lars Bergheim, Area Sales Manager at Reifenhäuser Cast Sheet Coating, explains: "The advantages of PAM speak for themselves - operation of the line becomes easier, scrap and energy consumption are significantly reduced, and product changes succeed in the shortest possible time. Since we first introduced the system last year, we have already successfully implemented PAM at several customers."
PAM is not only available for Reifenhäuser flat film lines, but also for third-party lines as an upgrade via Reifenhäuser Extrusion Systems.
Reifenhäuser Blown Film (BF) is presenting its latest blown film line concepts in Friedrichshafen. With the EVO Fusion technology the company offers a solution to one of the biggest problems in the use of recyclate in film production: on the one hand, ever higher proportions of recycled plastic are demanded, on the other hand, recyclate qualities fluctuate greatly and high-quality material is too expensive for many applications to produce economically. Thanks to twin-screw technology in the extruder, EVO Fusion can reliably process previously unusable, low-cost recyclates. This results in high-performance and, above all, profitable blown films for applications such as trash bags or mailing bags. A special feature of the EVO Fusion is direct extrusion, which eliminates the need for energy- and cost-intensive regranulation of the starting material. This means that fluff (film snippets) as well as all types of production waste and PCR material can also be processed directly.
"With EVO Fusion, we are adapting to the reality on the recyclate market and making blown film manufacturers independent of highly fluctuating recyclate qualities. Sustainability and profitability must go hand in hand - we supply the necessary technology for this," explains Eugen Friedel, Director Sales at Reifenhäuser Blown Film.