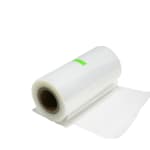
SABIC, a global leader in the chemicals industry, has embarked on a pilot project with Schwarz Group, Europe’s largest retail store operator, for the use of transparent film bags made from certified circular polyethylene (PE) in vegetable packaging. The project will include various different PE technologies from SABIC’s Trucircle™ portfolio based on materials produced via feedstock recycling of mixed and used plastic. Through this project 1 kg bags for organic carrots, made of flexible film using SABIC’s certified circular polyethylene, will be introduced between October and December 2020 by the retail group into selected stores operating under the Lidl and Kaufland brands in Germany.
SABIC’s Trucircle certified circular polymers in the pilot project include both low-density and linear low-density polyethylene (LDPE/LLDPE), high-density polyethylene (HDPE), and SUPEER™ metallocene polyethylene (mPE) resins.
“Our comprehensive strategy is to make all Lidl and Kaufland brand plastic packaging as recyclable as possible by 2025, thereby reducing overall plastic consumption by 20 percent,” states Dietmar Böhm, Managing Director of GreenCycle, which serves as a waste management and recycling service provider for Schwarz Group and other companies. “We strive to close material cycles and save resources.
“We have taken a big step forward on our journey towards building a truly circular plastics economy since we produced the first virgin-quality polymer materials from mixed used plastic back at the start of 2019,” explains Stephan Eltink, Director Polyethylene Europe at SABIC. “Our certified circular polymers are produced as part of our Trucircle portfolio that includes a wide range of polyethylene and polypropylene material grades, that can be drop-in solutions for applications in a variety of industries, including the food packaging industry. We are happy to welcome Schwarz Group among the growing number of downstream customers seeking to capture value from material sources that have traditionally been ignored or discarded.”
SABIC’s advanced feedstock recycling process recovers the material value of mixed and used plastic, including previously difficult to recycle post-consumer plastics, which could otherwise be lost to landfill or incineration. The waste is converted into an oil, which then enters the production chain just like fossil-based feedstock to deliver new materials without compromising on quality.
SABIC’s Trucircle portfolio, which showcases the company’s circular innovations and can help to provide manufacturers with access to more sustainable materials, spans design for recyclability, mechanically recycled products, certified circular products from feedstock recycling of used plastic and certified renewables products from bio-based feedstock.