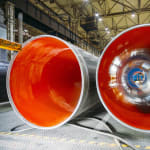
SABIC, a global leader in the chemical industry, today introduced Noryl AP2001G polyol for cast polyurethane (PU) applications. By partially replacing polypropylene glycol (PPG) or polytetramethylene ether glycol (PTMG), this oligomer of polyphenylene ether (PPE) improves the performance of cast PU systems by increasing both hardness and elasticity – properties that have been difficult to improve simultaneously until now. In addition, Noryl AP2001G polyol provides resistance to oils, moisture, abrasion, tearing and heat, helping cast PU parts withstand extreme conditions and potentially lengthen their useful life. Potential applications include mining drill bits, screens and protective pipe liners for slurry transport; components for hydraulic, robotic and conveying equipment; and wheels, casters and rollers.
“The development of Noryl AP2001G polyol in cast polyurethanes illustrates SABIC’s ongoing commitment to advancing material science to fill unmet needs across the value chain,” said Dr. Antonello Cerullo, senior business development manager, SABIC. “This technology provides multiple benefits for stakeholders. It offers formulators a new way to differentiate their products and can help end users to avoid costly downtime through the improved durability of parts and equipment. Also, by extending polyurethane’s pot life and slowing its reactivity, Noryl AP2001G polyol can give processors greater flexibility and more precise dimensional control while boosting productivity.”
The cast PU system is one of the most popular thermoset processes and the market is showing strong growth. According to Emergen Research, the increasing use of cast elastomers in the mining industry is the key driver of a CAGR estimated at 4.3 percent from 2019-2027. Other industries that use cast PUs are agriculture, oil & gas, material handling, and sports and recreation.
Validating Performance Properties
SABIC engaged Troy Polymers, a leading research and development laboratory based in Madison Heights, Mich., in the United States, to formulate PU samples using Noryl AP2001G polyol and conduct extensive testing and validation. Troy Polymers found that in both PPG- and PTMG-based PU systems, incorporating a small portion (13.3 percent) of NORYL AP2001G polyol resulted in a 10-point rise in Shore A hardness.
It also significantly increased both compressive strength and tensile strength compared to formulations without the SABIC product. Specifically, tensile strength increased nearly 3-fold (290 percent) for PPG-based PU and increased by 45 percent for PTMG-based PU. Furthermore, Noryl AP2001G polyol produced a 64 percent decrease in abrasion for PPG-based PU under standard test conditions. Immersion testing of PUs indicated that the addition of Noryl AP2001G polyol contributes to reduced absorption of either hydraulic oil or water after three days. Both systems absorbed less fluid, including 40 percent less water.
Polypropylene glycol is typically less expensive to use vs. PTMG; however, it usually results in lower-performing PUs because PTMG provides better hardness, toughness, stiffness, and tear and chemical resistance. The use of SABIC’s Noryl AP2001G polyol as a partial replacement for PPG helps elevate the properties of PPG to those of PTMG polyurethanes, enabling PPG to become a cost-effective, high-performing solution for PU formulations.
“At Troy Polymers, our business centers on driving polyurethane innovation and we’ve been able to validate that SABIC’s Noryl AP2001G polyol for cast polyurethanes is a true breakthrough technology,” said Aisa Sendijarevic, Ph.D., research director, Troy Polymers. “We observed impressive performance improvements in hardness, toughness and resistance to oil, water and heat for formulations that have been enhanced with Noryl AP2001G polyol compared to incumbent materials. These results show its strong potential to advance polyurethane technology well into the future.”