Besides saving energy and recycling plastic material, using less raw material is a key advantage both for the environment and for the customers. This is where foaming technology comes in.
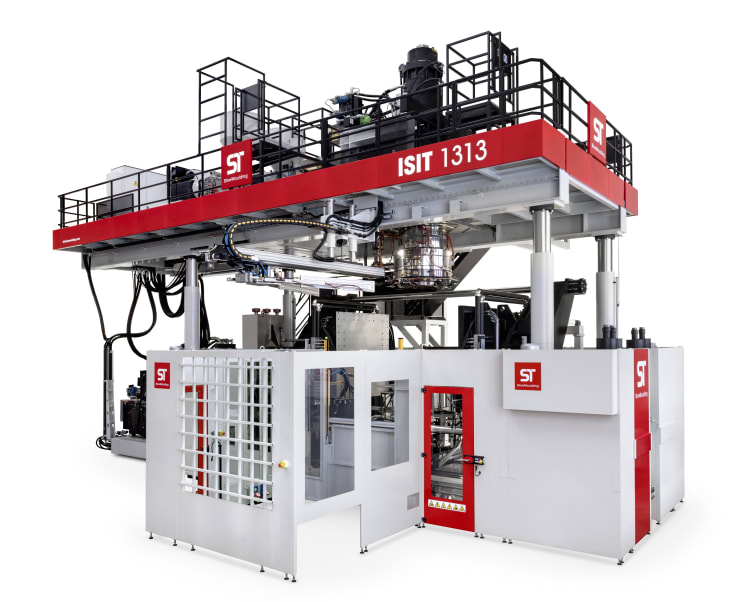
The successful ISIT model for the IBC production with ST proprietary Outer Coating Technology and PWDS
This technology generates a foamed structure into the blown part, using a neutral gas (N2 or CO2) and a nucleating agent. The density reduction results in lighter parts, raw material saving, better thermal and acoustic insulation. ST adiabatic extruders can be pre-arranged to feed the gas for the material foaming.
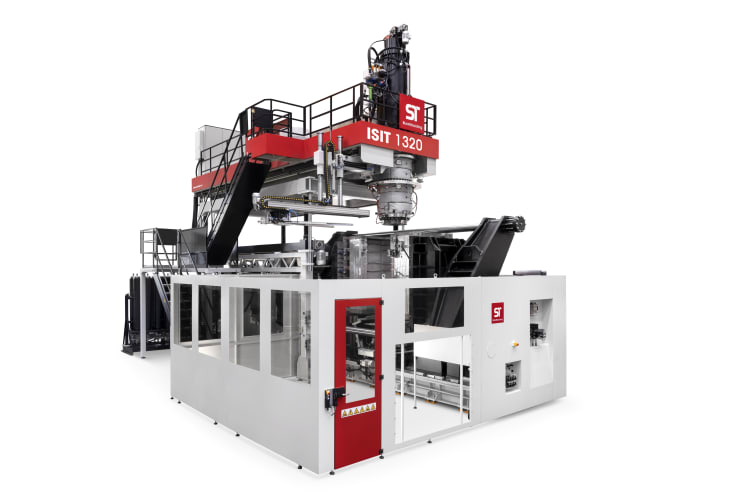
One of the ST bestsellers: the ISIT 1320 equipped with foaming technology
New frontiers are also involving the company in the development of advanced solutions for the Composite Pressure Vessels, including LPG, CNG and Hydrogen.
The future of climate protection is moving towards Hydrogen as an energy carrier. ST BlowMoulding is strongly committed to play a leading role in this challenge, by developing technologies for blow moulding hydrogen liners: a perfect match between expertise and market demands.
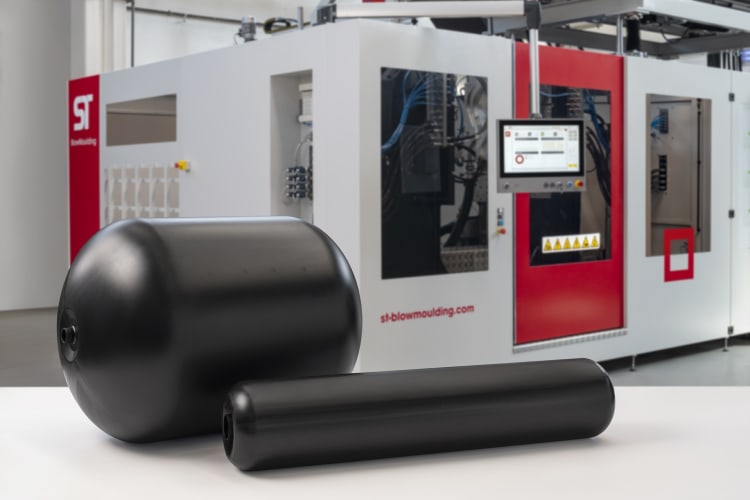
New market and applications: PA liners for hydrogen composite pressure vessels at 700 bar
Not to mention that ST still retains its market and technology leadership in the segment of the Suction Blow Molding with new and advanced solutions designed for the automotive industry, especially in the area of Coolant Lines for electric vehicles.
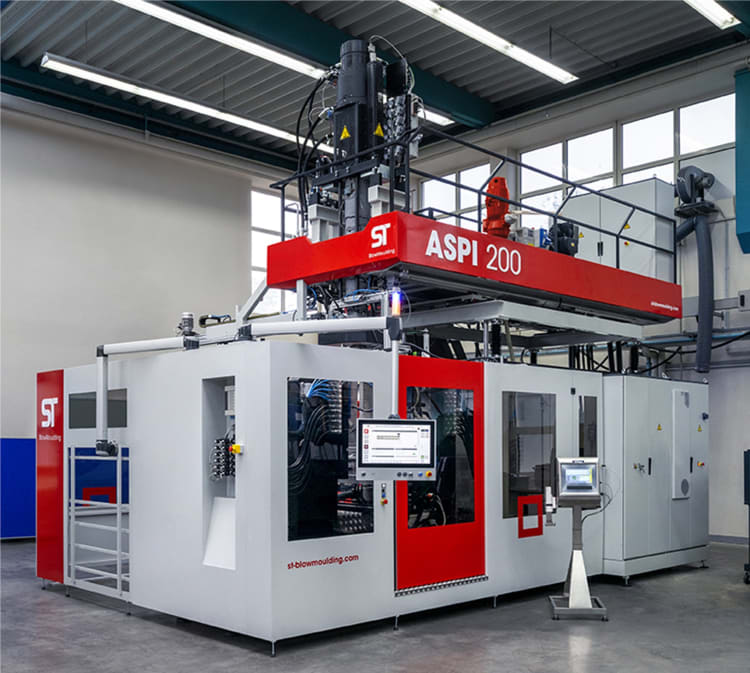
The ASPI model: the flagship ST suction blow molding machine
As a final remark, ST has always been very attentive to the machine ergonomics and being user friendly for the operators. This topic also matches the need for reducing the total machine downtime. That’s why the company has developed several solutions for quick head-tooling and mould changeover systems, including the patented hands-free Automatic Head-tooling Changeover (AHC) and other innovative solutions for small and large accumulator heads.
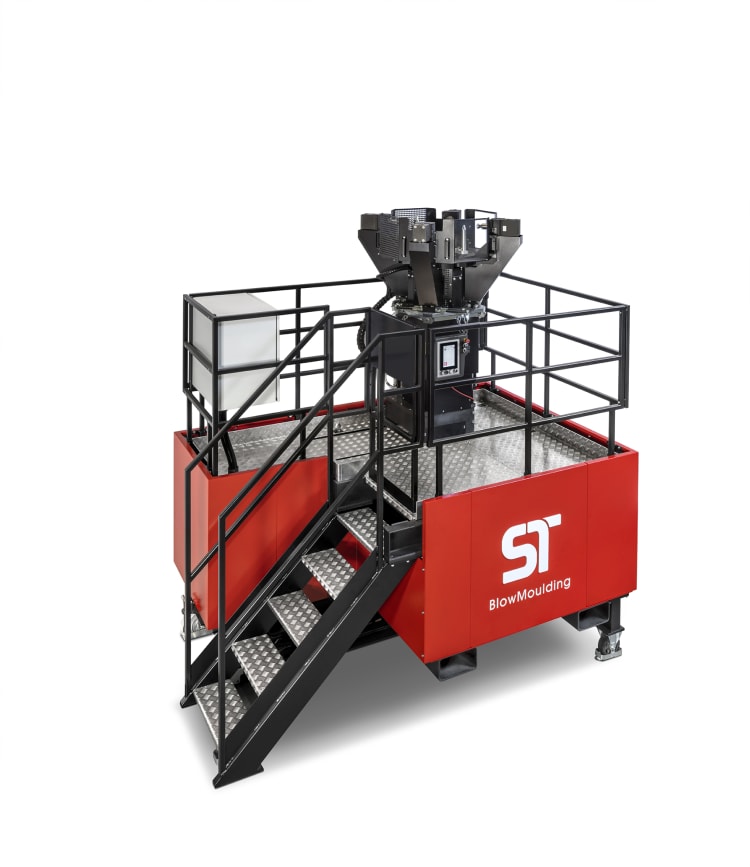
The ST proprietary AHC (Automatic Headtooling Changeover) is the new patented totally hands-free device
ST is also investing in technology and innovation regarding the automation and control. All ST machines are adopting IO Link sensors and actuators, they are all remotely connected and controlled, and they are all Industry 4.0 complaint. New advanced OPC UA protocols are adopted to download all the necessary SPC data.
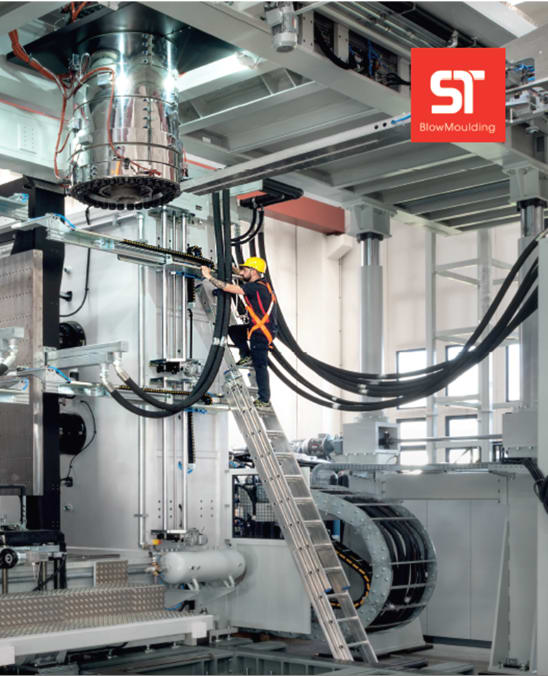
ST core competence is still in very large machine up to 3600 kN of clamping force and 90 L accumulator heads
ST BlowMoulding HMI and software is the most advanced in the market, as well as the most intuitive and user friendly. The control panel is continuously upgraded to satisfy all the customers’ needs with the newest programming innovations. The MyST is the ST App to be installed on your mobile device to monitor the status and the production record of your machine.
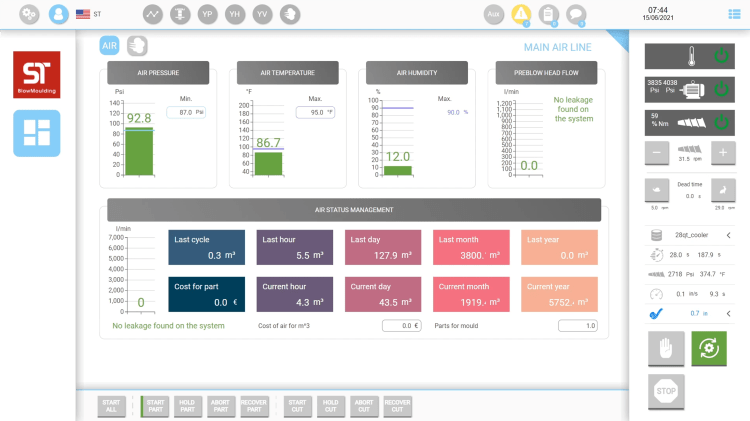
A screenshot of the newest ST control panel. A simulator is available for preview to all ST partners.
ST BlowMoulding is looking forward to welcoming you at the NPE 2024 to show more about the new Dual Head machines and discuss any blow molding topics of your interest!