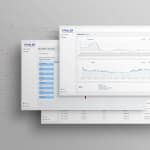
STADLER’s Service Data Cloud (SDC) provides a complete overview of the sorting plant’s operation with data captured from the facility’s equipment, unlocking opportunities to optimize its efficiency, facilitate troubleshooting and service support, and maximize uptime.
STADLER has developed in-house the SDC cloud-based platform, which captures operating and sensor data from the equipment at the customer’s sorting plant. The information is securely stored in the cloud and accessible from anywhere on- or off-site through a web portal. The SDC leverages automation and the Industrial Internet of Things (IIoT) to optimize and increase the efficiency of processes in STADLER sorting plants and provide better, faster support to its customers.
Amela Sijaric, Co-Head of the SDC Team, at STADLER says: “The SDC puts the customer and our Service Department in direct communication with the individual machines in the sorting plant. It provides valuable insights into the operation and enables us to work more effectively with our customer to resolve any issues as they arise, and to ensure that the plant continues to meet their evolving requirements effectively. The SDC is a tool with great potential, and we will continue to work with our customers to extend its capabilities with new functionalities.”
SDC is equally effective in all types of sorting plants and can be implemented at existing plants, where it may just need updating some hardware. In these facilities, it can highlight areas where the process can be improved and can be used to implement updates to the existing equipment.
Optimized process efficiency, maximum uptime
The SDC provides an overview of the operation of the sorting plant, with visibility on the individual machines. The data captured by the system is a powerful tool to enhance the sorting process, identify any bottlenecks or issues, and act to resolve them swiftly. Analysis of the historical data can help to optimize machine performance and reveal opportunities for improvements in the plant’s efficiency.
When there is an issue, with the SDC it can be resolved faster and more efficiently. “The system flags where the error is in the sorting plant’s flowchart, with a clear indication of the name of the device experiencing a fault,” explains Amela Sijaric. “The customer can see at a glance where to go to sort out the problem. If they need help with the issue, our technical experts can immediately access the machine data. They can understand the issue and provide a solution swiftly. This is particularly beneficial when the plant is a long way from STADLER Service Teams. By accessing the data, they can send the technician best suited to deal with the specific issue and take the parts they may need to resolve the issue.”
Downtime is reduced to a minimum by monitoring machine health and performance, and fast service - an important benefit for the customer.
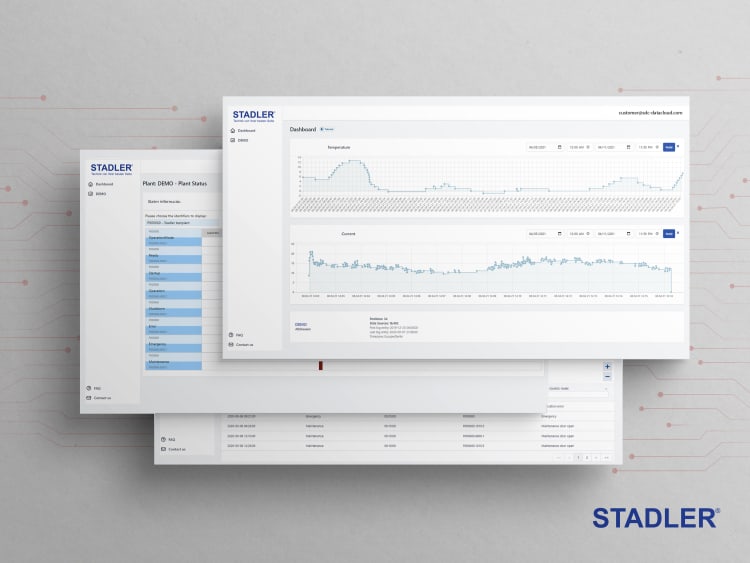
Full access to updated documentation and tutorials
The SDC has a section dedicated to providing customers with flexible access to a full library of documentation for each of the machines in their plant, so that it is always up to date. They include not only data sheets and operation manuals, but also a spare parts catalogue. When making an order, the customer will easily identify the correct part with the photograph, description and part number in the catalogue. The Documentation section also offers tutorial videos prepared by the STADLER Service Team, covering the maintenance tasks typically conducted by the customer.
Continuous innovation
The first pilot project started in late 2018 at a paper sorting plant in Ingolstadt, followed by other plants in Germany, France, Switzerland and Denmark. They include the AFM Entsorgungsbetrieb waste management facility in Feldkirchen, which has been using the SDC for the past six months. Mr. Anastasios Melidis, Chief Executive Officer of AFM sees the potential of the new platform: “It enables us to analyse our plant’s operating efficiency and recognize a loss of performance, as well as fast detection of errors or damage. It is also useful for our business, as it provides statistics that help us plan our operations.” He also found that “after a short introduction, SDC is easy to use.”
Mr. Christian Ascherl-Landauer, CEO of MAD Recycling GmbH, which has been piloting the SCD at its paper and cardboard recycling plant in Ingolstadt, Germany, agrees: “The operation of the application is practical and clear.” He has found that availability of the plant has improved since the beginning of the pilot: “The monitoring of the plant has improved. We can analyse downtimes better and make changes to the ongoing operation. Also, improved troubleshooting and targeted measures will improve availability further in the future.”
The development is ongoing, with new projects starting in Europe and in the USA. “We are looking at new functionalities, such as volume stream management and temperature analysis. We are also working to introduce condition monitoring and predictive maintenance functions, which will further reduce downtime,” concludes Amela Sijaric.