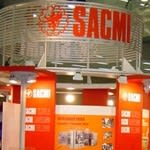
One hundred thousand specialised industry operators getting together with 1500 exhibitors, all with one precise ambition: to make “intelligent packaging” a reality, from raw materials to finished products. This, then, is the mission of Emballage, the packaging fair now in its 40th edition, to be held in Paris from 19th to 22nd November.
And it is integrated packaging solutions specifically designed for the needs of the beverage industry that will be playing a starring role in Sacmi’s display area. Here, in an area covering 1042, visitors can take a close look at the latest solutions to be developed by Sacmi Beverage, the Sacmi Division that, for some time now, has brought together the best of the excellent developments on the stretch-blowing, forming, labelling and filling fronts under an integrated production-marketing logic.
Systems for the injection production of PET preforms will be particularly evident thanks to the introduction of the new IPS: this latest Sacmi-developed system is characterised by flexibility and rapidity of size changeover, ergonomic solutions, energy savings, reduced overall dimensions and, lastly, a worldwide network of sales and after-sales services.
From preform production, then, to the new Sacmi SBF stretch-blowing machines, highly efficient, reliable tools designed to shape bottles the way customers want them. The rotary blowers in the SBF range have from 6 to 24 blowing stations and are at the very apex of their category, ensuring hourly output rates of over 64,000 standard half-litre bottles. One of the key advantages of this blower is the possibility of installing, on every machine in the range, a one-cavity mould for large bottles (up to 3 litres) or a 2-cavity mould for small bottles (up to 0.6 litres); moreover, the switch from single to double cavity (and vice versa) is extremely simple and is completed very quickly. Hourly output can therefore be as high as 2700 small bottles per station.
A development, then, that allows producers to make full use of the production capacity and potential of the downstream machine, an area in which Sacmi Filling specialises. Fully “Made-in-Sacmi” mechanical and electronic fillers that have been developed in the Parma industrial district to provide producers with the very best in terms of strength, reliability and production performance. Each machine stands out not only for its extreme specialisation and working flexibility (from carbonated drinks to hot and cold-fill products, from PET to glass) but also the ultra-clean filling technology, the automatic CIP system and the rapid format changeover: all in line with the most stringent safety standards.
With its unique capacity to design, coordinate and install complex plants, the Sacmi Group has developed considerable synergies by combining know-how in continuous compression technology for closures with innovations achieved in stretch-blowing: hence the arrival of the CBF (compression blow forming) range, forming units that can pass directly from resin to bottle, from raw material to container by making the most of the advantages offered by compression.
And that’s not all. There are also innovative labelling systems, where Sacmi provides high-performance, optimal-efficiency solutions designed at Sacmi Verona with the aim of making the labelling process better, more flexible and cleaner. Leading the way is the MOD (Modular) system, an effective response to labelling needs requiring more than one technology. Each module consists of a labelling station fitted on a mobile shuttle that can easily be connected/disconnected from the machine and replaced with another of different technology (Self Adhesive, Cold Glue, Hot Melt, Roll Fed) and performance. This solution requires far less factory space and also makes it easier to insert the machine on new and/or pre-existing lines.
Meanwhile, the Opera RFST series continues to go from strength to strength, thanks also to the Formsleeve+ system, which applies shrink-wrap labels directly from the reel of film. With RFST, labels are created and applied directly on bottles in a single seamless process, resulting in considerably greater efficiency and material, space and energy savings.
These are just some of the Sacmi-developed gems that will be flanking solutions for closure production, a field in which Sacmi leads the world thanks to its CCM (continuous compression moulding) machine range, which has enjoyed widespread market success on account of extremely short cycle times and very low energy consumption. These machines have now been improved even further and can provide output rates of 1600 caps per minute with just 48 cavities.