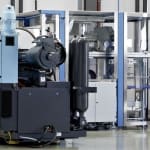
The Japanese-German company will be presenting its current new and advanced developments at the 21st Fakuma – International Exhibition for Plastics Processing – from 18 to 22 October 2011 in Friedrichshafen, as well as on the stand of a partner company.
Alongside sophisticated exhibits from all three machine series, the fully electric IntElect, the hybrid El-Exis SP as well as the hydraulic Systec, Sumitomo (SHI) Demag will for the first time be presenting the new NC5 plus controller. This controller offers users not only much greater convenience but also an increased range of functions. In accordance with the guiding principle of the 21st Fakuma to be a platform for the future topics of the industry, Sumitomo (SHI) Demag is also focusing on injection moulding of optical parts.
Three years after the merger between the injection moulding activities of Sumitomo Heavy Industries (SHI) and Demag Plastics Group, the Japanese-German company is presenting a harmonised range of machines which has been further optimised in terms of precision, dynamics and efficiency.
For instance, the fourth generation of fully electrical machines in the IntElect series is the result of a joint development between German and Japanese engineers. The IntElect offers high performance and availability, larger tie bar spacings and linear guides for high-volume and heavy moulds, making it ideal for the needs of the European market. Its excellent reproducibility with outstanding process capability values forms the basis for zero-error production. The series has been available with up to 4,500 kN closing force since autumn 2010.
IntElect: Zero-defect production for precision mass-produced articles from automotive electronics
As one highlight, Sumitomo (SHI) Demag will be presenting a fully automated cell for plug production at the Fakuma 2011, including a quality checking sequence for implementing zero-defect production. The high process consistency is demonstrated on the trade show stand by inline statistical quality analysis including calculating the process capability analysis Cpk.
At the trade show, an IntElect 100-340 (1,000 kN) will manufacture two-pin plug casings made from glass fibre-reinforced PBT in a four-up hot runner mould made by Fischer GmbH & Co. KG, Sinsheim, in a cycle time of 11 s. The component, weighing only 3.5 g, is intended for automotive electronics and has significant differences in wall thickness. It imposes very great requirements on precision and reproducibility.
The linear robot SDR 22 from the company's own product portfolio is used for removing the moulded parts, and its operation is directly integrated in the new NC5 plus machine controller.