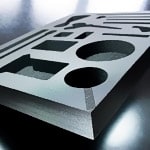
Sekisui Alveo, manufacturer of polyolefin foams, has answered the growing wishes of the packaging industry with an expanded colour palette of Alveobloc. Since March, the block foam has been available in blue, yellow, grey, green, red, and black. Alveobloc is already being used successfully for transport packaging. With the new colours and higher UV stability, increasing use in product presentations and displays is expected.
Greater choice for packaging designers. Alveobloc by Sekisui Alveo ensures reliable transport protection and offers great design freedom. The material is suitable for all types of converting, including e.g. grinding, die cutting, or water-jet cutting. The new colour palette of Alveobloc gives more opportunity for design ideas, because every packaging designer knows: bold colours grab attention, arouse emotions, and can optimise a sales presentation. The foams also meet all normative requirements for packing materials.
Interesting design elements. The foam skin of Alveobloc with its uniform and even surface offers new design options for designers and developers. Also the texture of the cut cells of the foam can be used effectively as a design element. Alveobloc can be used to design individual and attractive padded inserts for high-quality merchandise just as well as solutions for suitcase liners or reusable packaging.
Secure transport. The odour-free block is made from Alveolen, physically cross-linked sheet foam: With hot air the foam is laminated into a block with a guaranteed material thickness of 100 millimetres. Each layer has a uniform closed-cell structure; the mass is distributed evenly throughout the entire block. Thus Alveobloc offers very good cushioning and insulation and fulfils the individual protection requirements for a wide variety of products.
Time as a competitive edge. When it comes to converting, ordering Alveobloc with exact 90-degree angles, flat surfaces, and all edges squared is an advantage: The foam blocks can be processed directly without time-consuming preparation. Furthermore, Alveobloc is free from silicone and inorganic fillers such as talcum or chalk, so there is no need to clean silicone residue from the processing equipment, and there is no heavy wear from the use of hard fillers. Because of the closed cell structure, water absorption is held to less than one percent, meaning that after water-jet cutting the material no longer requires an extensive drying process. "If you look at the entire process chain – from receiving to processing to delivery – then you realize that Alveobloc significantly reduces work for converting companies, and thereby helps to save time and money", explains Oliver Bürklin, responsible Market Segment Manager at Sekisui Alveo.