With the expertise of Happ in the area of plastics injection molding production and its many years of experience in conveying and automation technology, various modules are being developed which ErgoTek can use flexibly and in a modular way in the conveyor technology systems. Here, special attention is paid to the products’ cost-efficiency.
A project recently completed by ErgoTek in the company’s own production is the flexible linking of two EcoPower machines by conveying systems with buffer capacity. With this system, the outer and inner tubes of oil filter drain screws for the automotive industry are fully automatically assembled, inspected, laser-printed and deposited.
In this system, two EcoPower 110/350 machines are integrated, both with 1,100 kN clamping force and each equipped with a W818 robot from WITTMANN. On these machines, the inner and outer tubes of the oil filter drain screw are injection-molded, each with a 2-cavity mold, then removed by the Wittmann robots and presented to a camera to check the parts’ dimensional accuracy. Another camera examines the parts for burr formation. Next, the tubes are transported further by FlexiTek conveyors from ErgoTek and buffered for cooling. Then, a Scara robot fits the outer tube onto the inner tube. With the help of an articulated robot and a further camera check, the depth gauge and angular position are measured, and subsequently the parts are transferred to a labeling band for laser printing. From there, the finished components are transferred to the Flexi buffer from ErgoTek.
Using this clocked system has finally made cost-efficient manufacturing of this product possible. But the production cell offers a number of other advantages as well:
- Thanks to interlinking the two parts of the system via the FlexiTek conveyor belts, storage of the individual parts can be dispensed with, and the allocation of cavities and consequently traceability remain ensured.
- SPC parts can be requested and removed via the chutes.
- If an interruption occurs on one system component, the other components can continue their production for up to a maximum of one hour.
- The box buffer with the finished parts only needs to be emptied about every 2.5 hours.
- The linkage of the FlexiTek conveyor belts requires only a minimal control effort and permits separation of the individual safety areas from each other.
Happ has been relying on technology from Wittmann Battenfeld for over 15 years. What is specially appreciated at Happ and ErgoTek is the robustness and simple operation as well as the easy extensibility of Wittmann Battenfeld equipment, in addition to the excellent service. Dirk Wevelsiep, Sales Manager at ErgoTek, comments: “Thanks to their easy extensibility, the injection molding machines from Wittmann Battenfeld are ideally suited for intelligent linkage. And when it comes to aftersales service, Wittmann Battenfeld is also in a strong position.”
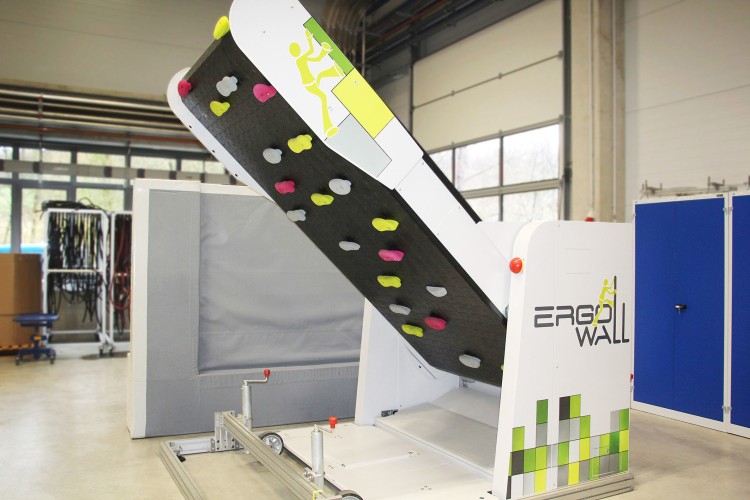