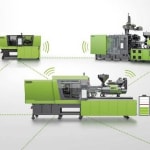
In many cases, wristwatches require sales packaging that is not just high quality, but original - in the form of globes, for instance. Over the four days of the trade event, ENGEL will use a mould supplied by its customer Betar to produce base bodies for globes on an ENGEL victory injection moulding machine. Hemispheres that can be put together will be moulded. Based in Chistopol (midway between Moscow and the Urals), Betar manufactures numerous products for gas and water metering and a great many plastic articles for customers.
Flexibility is an essential characteristic of the company’s production equipment, which is why the company mainly invests in tie-bar-less injection moulding machines from ENGEL’s victory range. “Free access to the mould area makes it much quicker to install and remove moulds,” stresses Olaf Kassek, Managing Director of OOO ENGEL in Moscow. “Thereby, tie-bar-less technology significantly improves the availability of injection moulding machines when producing small batch sizes.” Tie-bar-less technology also enables compact manufacturing cells, which is especially advantageous when producing complex, three dimensional parts and using multi-cavity or multi-component moulds. In such cases, the moulds have a large volume and the injection moulding process tends to require relatively small clamping force thanks to rather short flow paths. Tie-bar-less technology makes it possible to choose the machine size on the basis of the clamping force actually required, rather than the mould size. Given that mould fixing platens can be used to the hilt, even small injection moulding machines can be fitted with large moulds.
Consistent processes despite variable pellet quality
The victory machine on show in Moscow will have a new generation injection unit. On the basis of its extensive experience across the many different application areas for its injection moulding machines, ENGEL has restructured the sizes of the hydraulic injection units and further optimised performance data such as injection pressure, injection speed and plasticising performance. The long established ENGEL servohydraulic ecodrive is standard equipment in the new machine models. Depending on the type and size of machine and the application, this cuts the energy requirement by 30 to 70 percent. Key to this is needs-based pump capacity. When a machine is idle (for example, during cooling phases), the engines also close down and consume zero idling energy. As positive side-effects, the machine runs much quieter and the hydraulic oil is not heated as much, which reduces the amount of energy needed for oil cooling.Visitors to the trade fair will also be able to track the workings of iQ weight control live on the control panel of the victory machine. During the injection process, the software analyses the pressure profile in real time and compares measured values by means of a reference cycle. For every shot, the injection profile, switchover point and the holding pressure profile are automatically adapted to current conditions and the injected melt volume is kept consistent throughout the production operation. This compensates for fluctuations in environmental conditions or moulding compound before rejects can be produced.
The injection moulding machines in the victory and e-victory series enable compact manufacturing cells and highly efficient automation concepts thanks to their barrier-free clamping units.