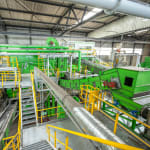
Immark AG, part of the Thommen Group, is a pioneer and market leader in the recycling and disposal of electronic waste in Switzerland with a recycling rate of up to 95% that far exceeds the requirements of the European Waste Electrical and Electronic Equipment Directive (WEEE). The company chose Stadler to design and install a new sorting plant to replace its existing facility in Regensdorf.
“It is the largest processing plant for electronic waste in Switzerland and it must ensure high throughput and capability to process the volumes we receive,” says Patrick Wollenmann, Project Manager at Immark. “We expect that with this new plant, we have laid the foundation for a successful future in terms of operational management.”.
The new facility features innovative design and the latest technology, and is in fact the first electronic waste sorting plant to use a ballistic separator. The plant operates in a 2-shift service with a capacity of up to 12 tons per hour, meeting Immark’s requirements of greater capacity and better purity of the output. It also optimizes the recovery of printed circuit boards.
“For us, Stadler´s convincing technology of the conveyor belts and ballistic separator, and their proximity to Zurich were decisive. We also appreciate very much the work of the competent project managers, the quick and constructive implementation and solution-oriented approach,” says Patrick Wollenmann.
“The Stadler STT5000 ballistic separator pre-sorts the material into three different fractions. It separates the material into fines, flat plastics and cables, as well aa cube-shaped material such as electronic motors,” explains Jan Dollenmaier, Stadler joint Project Manager.
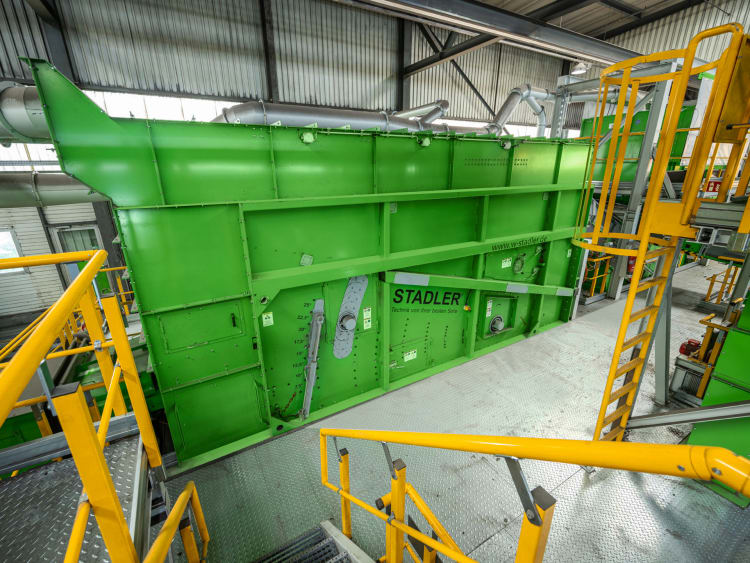
Innovative plant design for exceptionally high-quality output
The new sorting plant receives materials in WEEE Directive Groups 1-3 (Large – Small Household Appliances and IT Equipment) and 4 (Consumer Equipment), which are processed in several different processing modules. The modules are positioned in line, but are also equipped with separate feeders for independent usage, which results in higher availability of the whole plant.
The flexible modular design of the plant allows the adjustment of the machines throughout the process to ensure consistently high-quality non-ferrous, ferrous, PCB, stainless steel and plastic fractions.
In the first module of the process, the infeed material is manually sorted to remove the toxins and hazardous components, as well as valuable materials such as cables, printed circuit boards and metals.
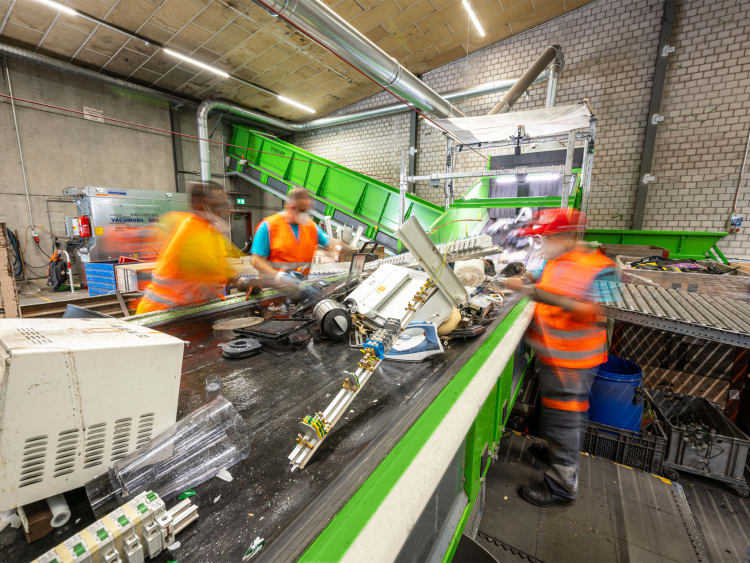