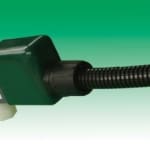
Traditional methods of decorating or labelling products include printing directly on to the item. This is often referred to as pad printing and is both time consuming and messy, as well as of inferior quality. Labels can be printed and then stuck to the product. Again, this is time consuming and manufacturers run the risk of using poor quality adhesive that will result in the labels peeling off. One of the main benefits of IML is that a complete step in the production cycle is eliminated, saving both time and money. As the label is attached to the product at the injection moulding stage, no secondary process is required to print on the product or to stick on the label.
UB Plastics manufactures millions of plastic moulded products for the brewing industry every year. At its factory in the UK, all mouldings are carried out in-house and printed using a variety of different methods, depending on both the product and the budget.
Recently, it has been developing tamper-evident bungs for major breweries to safeguard the beer while in transit and when stored. Quality is extremely important for these companies and UB Plastics is always looking for ways to improve the products it supplies.
- The first in-line system was set up here in 2003.” explains Andy Cox from UB Plastics. - Although the technique had been used in the medical industry for a while, it was new to the markets we supply. We always want to ensure our customers get the best possible products and IML helped them and made us more competitive.
Now, the company has two major IML lines, manufacturing the tamper-evident bungs. The latest line comprises an Enaiviv injection moulding machine together with a robotic arm system and label magazine. In this system, eight caps are manufactured at one time.
The cut, pre-printed labels are placed in a magazine at the side of the injection moulding machine and transferred under vacuum to the moulds. However, in these circumstances, when the vacuum is switched off before the polymer is injected into the moulds, the labels will drop out. There needs to be a way for the labels to remain in position. This is where static generation becomes a vital part of the IML method.
Although a relatively simple process, there are pitfalls for any company wanting to set up an IML system. Meech’s systems engineer worked with UB Plastics to ensure that the process went smoothly and helped solve particular issues pertaining to the label material and the vacuum transfer.