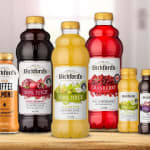
To remain competitive in the dynamic beverage market, Bickford’s in Australia reached out to Sidel to launch two new PET formats for its premium syrup and juice brands, to complement previously designed & commissioned 1 litre formats. Sidel experts conducted the line conversion with its latest remote solutions, in just two days for each new format. In addition and to respond to Bickford’s commitment to product quality and safety, Sidel showed great versatility by also carrying out the maintenance of the Aseptic Combi PredisTM remotely, while optimising line efficiency.
Founded in 1839, Bickford’s is an independently owned business under The Bickford’s Group with its head office based in Adelaide, South Australia, and is one of the oldest and most treasured Australian brands. The company enjoys premium positioning in the market and owns a wide product portfolio of non-alcoholic beverages, encompassing carbonated soft drinks (CSD), juice, cordials, syrup, flavoured and plant-based milk, and flavoured water. Every product from Bickford’s shows great commitment to excellence and outstanding quality.
Bickford’s was already equipped with a complete flexible PET line from Sidel, managing both sensitive products and CSD via an Aseptic Combi Predis™ and a Combi SF300, respectively. With the trend towards premiumisation, it is crucial for beverage brand owners to focus on flavour variety and product diversification in the market while maintaining safety. Thanks to a successful partnership on the 1 litre formats, Bickford’s reached out to Sidel again in order to introduce two new formats that would further increase their market share & category penetration and to perform maintenance for excellent product safety.
The right remote support to facilitate fast line adaptation and maintenance
Sidel supported the customer to reach their ambitions with highly skilled experts and two advanced remote solutions: Remote Video Assistance (RVA) and Remote Access. Despite all the pandemic-related restrictions, everything was delivered on time with impact.
Bickford’s flexible complete PET line was tuned-up for introducing smaller format variations of two 1 litre PET bottles originally designed by Sidel in 2019 – adding a 500 ml option for Bickford’s premium syrups & flavoured milks and a 250 ml format for their premium juice brand.
Taking advantage of real-time video assistance, Sidel experts empowered the Bickford’s team to implement the best line configurations, with regards to products dependent parts and moulds etc. Remote Access to the customer blow moulder, filler and labeller was also leveraged by the Sidel team to optimise recipe process parameters. In addition, the Bickford’s team benefitted from Sidel’s expertise in maintaining top line efficiency and ensuring overall packaging quality was produced with a high degree of accuracy using the remote solutions. This process focused on the optimisation of bottle conveyancing and the control of efficient machine operations.
To keep up with high product safety, 100 Clean In Place (CIP) cycle maintenance was also carried out remotely. Following careful guidance with RVA, the maintenance of Bickford’s Aseptic Combi Predis™ from disassembly, spare parts replacement, reassembly to testing and validation was accomplished in only three days.
“Then to validate that the line was running at its maximum uptime, we proceeded with production assistance. We are glad that the customer is satisfied, and they have already planned the next remote 200 CIP cycle maintenance. This open partnership approach based on constant and regular touch points with the Bickford’s maintenance team is a real lever to efficiently support them in achieving their goals” concluded James Terry, Service Account Manager at Sidel.
“Time was precious to fulfil our market commitments. Sidel’s solid and prompt remote support empowered us to achieve the line conversion and the 100 CIP cycle maintenance with minimal downtime. These were great outcomes for our team. The strong knowledge foundations acquired by our technicians from previous Sidel training, together with the excellent expertise transfer enabled by their digital solution during these projects, was a formidable combination to keep on upskilling our team” commented George Kotses, Operations Manager at Bickford’s.