Multiple needle closure system for maximum part output in minimal space
Kebo AG, Neuhausen am Rheinfall, supplies the 16-cavity mould for the production of insulin caps at the Fakuma exhibit. With the trend in medical technology targeting ever-smaller part geometries and weights, comprising critical tolerances and high complexity, the Swiss family-owned company unveils a new Multivalve system. Meeting increased demand for needle-valve systems, it offers first-class sprue quality, high production volumes - due to the proven Kebo cluster design (pitch circle diameter 60 mm - and a compact tool to fit within the smallest possible injection moulding machines. It also impresses with its long service life and high ease of maintenance.
In this Multivalve system, the development team succeeded in maintaining the space requirements of the existing open, compact, needle closure cluster arrangement. The tiny cavity spacing delivers maximum part output for a tool surface of this . The exhibition will show the highest expansion stage with eight cavities per cluster. Four or six cavities are also feasible, depending on the part geometry and the injection position. Uniquely, the system can also easily and safely place individual cavities.
Since the medical market typically demands all-electric solutions, especially in cleanrooms, Kebo actuates the needle closure nozzles via an electric plate. As well as the high precision, cleanliness and process reliability, the solution delivers compelling high repeatability, lower wear and very good temperature control. Additionally, the needle speed is individually adjustable. As an alternative to the electric needle closure, a pneumatic actuation of the drive is available.
Cleanroom control regulated for predestined medical technology applications
Controlling the hot runner needle closures in the mould, Kebo deploys the M-Ax control unit engineered by Mold-Masters, Baden-Baden. This unit opens and closes the hot runner needles at defined speeds and movement profiles, monitoring the end position. Its Tempmaster series controller is very flexible, can be set up for any application and doesn’t require programming knowledge. Controlling all linear (e.g., core pulls, ejectors) and rotary axes (e.g., index plates, rotary plates), the all-electric M-Ax unit is ideally suited to cleanroom environments and therefore regulated medical applications.
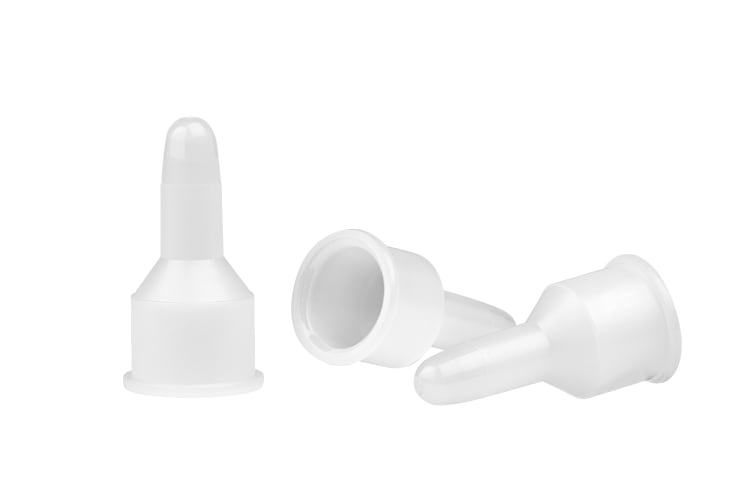
M-Ax offers maximum accuracy and the simplest automated tool customisation options. The servo-axis control functionality can be combined with up to 256 temperature-control zones. Up to 64 inputs and outputs are feasible, offering complete control of all injection moulding functions. Additionally, the controller is very efficient, consuming up to 60 percent less energy. This is due to the servo drives, which only require electricity on movement. One device can be used for several tools, increasing its flexibility. In addition to the compact design, the touchscreen featuring large symbols delivers easy operation and user-friendly, intuitive servo and temperature control.
Easy-flow, performance-optimised, medical-safe PP copolymer
Plastic granules used at the booth are especially suitable for medical applications, characterised by a melt flow rate of 70 g/10 min to facilitate complete filling of the 16-cavity mould. Supplied by Borealis AG, Vienna, Sumitomo (SHI) Demag previously cooperated with this partner to successfully tested pipette tips using the trademarked Bormed material, highlights Sattel.
A high flow hetero-phasic PP copolymer specifically developed by Borealis supports healthcare customers comply with EU medical device (MDR) and in vitro diagnostic (IVDR) regulations, thereby increasing patient safety. Offering a better flow and high impact strength, from a machine performance perspective, the high flow ability of the material optimises the production cycle time.
Sattel concludes: “Since our last major exhibit, the medical sector has faced some significant pandemic challenges, in addition to the introduction of new EU medical device regulations. Despite this, our industry-focused sales structure has enabled us to respond swiftly and apply our industry competence and expertise in a much more targeted and efficient manner for the benefit of our medical customers. Additionally, our collaboration program with our major industry partners continues to support transformative projects, maintaining SDG’s preferred partner position and conveying our longstanding message that we are the “easiest to work with.”