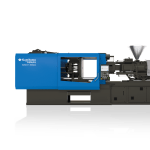
This October, the Sumitomo (SHI) Demag packaging team will showcase how the shift to all-electric in the company’s machinery portfolio is supporting fast-cycling mass-packaging manu-facturers to more than halve energy consumption, while simultaneously increasing output.
Manufacturing packaging has always been about balancing processing speed with cost. Now, the sector is also tasked with reducing environmental impact. As an early world leader in all-electric efficiency, the main Sumitomo (SHI) Demag packaging exhibit at Fakuma 2024 will demonstrate how the high speed IntElect S series is helping processors to save resources and increase performance in the most energy-efficient, economical, space and timesaving way.
Processing packaging materials in the most efficient way directly addresses one of the major operating expenses for mass-packaging moulders - energy consumption. “The on-going innovations happening in injection moulding are indicative of just how much efficiency and sustainable value are aligned to current and future packaging trends”, reports Director Business Development Packaging, Arnaud Nomblot.
“Fluctuating energy costs create uncertainty. Particularly for packaging manufacturers where energy is the highest and most unpredictable expense. To counteract this, fast processing repeatability and reduced waste, combined with halving energy costs is now regarded as imperative,” highlights Arnaud Nomblot.
Utilising direct drive technology underpins the Group’s packaging strategy. Until recently, matching the force and speed of hybrid packaging machines was inconceivable. But, with more than 80,000 all-electric machines now installed globally, Sumitomo (SHI) Demag has fused all of this market expertise with application knowledge to edge ahead and give packaging processors the blend of productivity, reliability, and energy savings.
To help put the opportunities into context at Fakuma 2024, on the main booth (B1-1105), Sumitomo (SHI) Demag, with a selection of trusted partners, will demonstrate how the IntElect S series outperforms previous generations of packaging machines, yet assists processors of narrow tolerance and thin-walled packaging lids and containers to more than halve energy use.
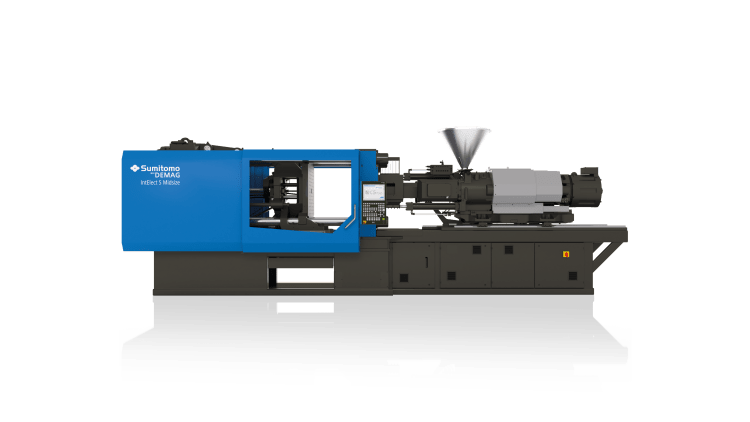
Faster and more efficient
This year’s packaging exhibit features an IntElect 2 S 220/660-1400, efficiently manufacturing four deco-rated food containers made from PP, with an integrated IML side entry robot. All in under four seconds. “Cycle times for the all-electric S series start at around four seconds,” emphasises Arnaud Nomblot. “The optimisation of tool movement, nozzle position, metering speed, injection and ejector movements increases productivity significantly. The combined cost savings and increased throughput can, in some cases, lead to a ROI of 18 months”, claims Arnaud Nomblot.
During the live exhibit, the IntElect S 220 ton machine will manufacture IML 250ml dairy and spread con-tainers with a shot weight of 45 grams on a four-cavity mould tool supplied by Société Nouvelle Caulon-que. Seamlessly feeding labels with precision into the packaging machine is an automated IML system supplied by Pagès Group, with iPB Printing B.V. supplying the high quality labels and TotalEnergies providing the material.
“Combined with the PAC-E series, which halves energy costs for mass-manufacturers of beverage caps and thin walled packaging, the associated benefits of all-electric technologies are now even more widely available to packaging applications”, notes Arnaud Nomblot. A 350 ton PAC-E machine is launching globally very soon, immediately followed by the 420 ton.