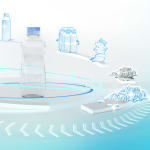
One thing is beyond doubt: how the human race deals with packages and recyclables is going to have to change significantly in the future – away from resource consumption and towards a sustainable closed-cycle economy. While this thinking is only gradually gaining acceptance, Krones is already several steps ahead. Because the technology corporation’s solutions have meanwhile progressed way beyond the first cycle. Why? Because they keep packaging plastics in a closed circuit. Disposable products like PET bottles thus get a chance for a sustainable, eco-compatible life –not just once, but repeatedly.
Holistically conceived package recycling
Millions of PET bottles a year are already being recycled on Krones’ MetaPure systems – depending on the demand involved, in different material qualities up to and including food-grade PET. Because the company is pursuing a holistic approach, it is step by step expanding its technology to cover additional types of plastic. The MetaPure W washing modules can already be used not only for PET, but also for processing polyolefins (PO). The module’s pre-washing component will be on show at the K 2019, and there even permit a view of its internals. In order to equip its clients with application-tailored turnkey factories, Krones cooperates closely with Stadler Anlagenbau GmbH to equip its customers with precisely tailored turnkey factories. The company is one of the market leaders in the field of sorting systems and has already sold more than 350 turnkey systems and 2,000 individual components worldwide. At the Krones stand, experts from both cooperation partners will be happy to discuss the concrete synergy effects and overall solutions that will result from the collaboration.
Fast, energy-economical container production
Handling preforms with a recyclate content of up to 100 per cent? With the Contiform stretch blow-moulding machines, it’s no problem. The high-speed version from the series, the Contiform 3 Speed, is represented at the K 2019 by a blow-moulding station. With a station output of up to 2,750 containers per hour, it produces application-tailored packages for still water, CSDs and sensitive products. Like all machines in the Contiform series, it has been designed for high energy- and media-efficiency. It undercuts the already-very-low energy- and compressed-air consumption of the Contiform 3 Pro by another up to 15 per cent.
Direct printing as part of the cycle
High-quality printing on recycled containers, and complete recycling of printed containers: how even digital container dress can be integrated into the recycling flow of PET will be demonstrated live at the fair by Krones’ subsidiary Dekron: with a laboratory machine based on the technology of the DecoType Select direct-printing machine. This will on the stand be printing on containers which are made 100 per cent from rPET – and which nonetheless are not lost to the reusable-material cycle. As the APR, the American Association of Plastic Recyclers, had already confirmed last year, the ink used can in the recycling process be removed again from the PET without leaving any residues. For users of this technology, direct printing opens up more freedom in terms of packaging design, since firstly it boasts a high colour brilliance and options for printing on embossed and structured surfaces, thus creating an attractive combination of look and feel. And secondly, it is possible to alter motifs literally at the touch of a button, and new or daily updated marketing strategies can be implemented in next to no time.
New technology for preforms
In the shape of MHT Mold & Hotrunner Technology AG, Krones is deploying another subsidiary in Düsseldorf. The company has belonged to the group since 2018, and specialises in manufacturing PET tools and post-treatment systems for producing preforms. Its performatively excellent high-tech injection-moulding tools image all preform designs and threads in common use. They are suitable for almost all machine platforms known on the market. MHT will be showcasing the latest coup landed by its in-house innovation incubator both on the Krones stand and its own – Stand C42 in Hall 1: an innovative hotrunner technology that even with a flake content of over 70 % rPET achieves outstanding results, excelling not least in terms of particularly homogeneous temperature control of the melt, and natural balancing. The construction has enabled the balancing and rerouting of the melt flow to be designed-enhanced and improved.
Eco-friendly, resource-economical container design
The ideal package offers persuasively attractive pluses in all situations: in the production process and at the point of sale, during transport and finally during recovery as well. Since Krones has signed up to providing holistically conceived solutions, development work on both bottle design and machine technology goes hand in hand. It is only when both these aspects supplement each other to perfection that the best solutions are arrived at – for producers, consumers and the natural environment alike. Krones’ packaging designers optimise existing designs in terms of weight, haptics and line efficiency. And they can draw upon profound expertise in ecological and economic requirements, like choice of materials, recyclability, or weight optimisation. The results and benefits can be viewed at the fair directly at the object involved – exemplified by a selection of current design studies and customer projects. These also include Flip Lid: an entirely innovative packaging system jointly developed by Krones and Aptar. Because it lastingly joins closure and bottle to each other, it prevents the lids being carried over into the natural environment, and ensures that beverage bottles are completely recovered.
Source: Krones