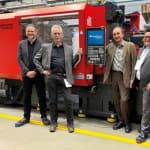
Renowned Swiss hand tool manufacturer - PB Swiss Tools AG - recently installed one of the most innovative injection moulding solutions at its production facility in Switzerland. Designed to boost productivity and maximise manufacturing precision, the fully-automated system validates Sumitomo (SHI) Demag’s expertise in engineering highly complex, multi-component moulding cells.
A fully collaborative effort , the cell comprises an efficient, energy saving IntElect 350 ton Injection moulding machine. Equipped with the company’s latest multi-component moulding technology, it can mould three different materials, including MuCell for the inner part of the tool handle. Following a four-step process, the cell uses an ABB 6-axis robot coupled with an index plate drive to seamlessly rotate, present and remove the component after each overmoulding stage is complete. Acceptance of the plant in Schwaig took place at the end of May 2024, followed by delivery to Switzerland in July. Commissioning is scheduled for the end of August.
Early technology adopters
PB Swiss Tools is seen as a "lighthouse customer" in Switzerland reports Urs Kocher, Project Manager of Mapag Maschinen AG, Bern, the company that represents Sumitomo (SHI) Demag in Switzerland. “We are immensely proud to have supported such a prestigious customer. This was only possible thanks to the hard work and diligent efforts off all parties involved - from project planning to implementation and delivery to the customer. Sumitomo (SHI) Demag was able to provide its expertise as a prominent leader in all-electric injection moulding machines, multi-component technology, special applications and automation,” adds Kocher.
The production line epitomises flexibility. As well as manufacturing new, ergonomically shaped handles for new products, the line is also able to manufacture a wide variety of handle s from the existing PB Swiss Tools product portfolio. For most products, the inner part of the handle is moulded using MuCell foam technology to reduce weight and increase dimensional stability. The handle core is then overmoulded with a rigid material to increase stability and strength. The process finishes with the application of a TPE overmoulding to give users a softer, more ergonomic grip. Using gripper recognition, each phase of the overmoulding process selects the correct tool data instructions and material shot weight. This alone was a complex challenge to navigate due to the mould tool set up and variety of polymers used.
At the heart of the fully-enclosed production cell is an IntElect 350/830-1100H-450L-450Y machine. Delivering maximum precision with parallel, dynamic movements, the large mould space combined with high tie bar clearance, optimises the working envelop. "In principle, there are four moulding and overmoulding stations," explains Klaus Rahnhöfer, Senior Business Development Engineer of Automation & Robotics at Sumitomo (SHI) Demag. Mr. Rahnhöfer is a proven expert in multi-component technology, with a wealth of experience in tool and mechanical engineering, plus integrated automation solutions. Both Kocher and Rahnhöfer designed and executed the project from start to finish.
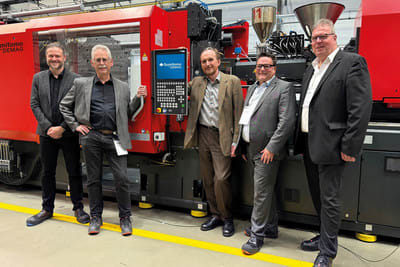
The multi-step process
At station one on the operating side of the production cell, the centre core of the tool handle is made using the MuCell foaming technique. When the tool opens, the ejector moves forward and lifts the plate, rotating it 90 degrees counter clockwise. The ejector returns and the tool closes. "The parts are placed in the next station by retracting the index plate," Rahnhöfer explains.
Station two is the L-injection unit. This is located in the lower part of the tool. Here, the inner handle grip cores are overmoulded with a harder material to increase stability and strength. After opening, the ejector advances and lifts the plate, rotates it another 90 degrees counter clockwise, returns and closes the tool again.
Station three is the Y-injection unit. Here, a soft component made of TPE for high grip torques is applied to the product handle. Finally, at the fourth station, each part is stripped by a hydraulic core pull and scraper. This stage is located at the top of the mould tool where there are no contoured inserts. This allows the mould to remain closed so the three injection processes can continue running uninterrupted. “The handles are mounted on both sides of their spines so they can be stripped and removed by the robot," clarifies Rahnhöfer.