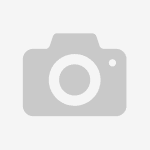
Many wage-intensive jobs have been transferred to Eastern Europe and Asia and new technologies have been introduced. Purposefully utilizing the key technologies, electrical discharge machining and milling, is therefore equally relevant for manufacturers and users of such machines.
EDM and high-speed cutting (HSC) are among today’s key technologies for classic tool and mold machining. While the electrical discharge machining method works by thermal removal, high-speed cutting is a method of cutting with a geometrically defined cutting edge.
Even from this simple and hardly noteworthy comparison it can be seen that there are characteristics, which determine the basic suitability of the method for certain applications.
The term high-speed cutting typically means machining with a geometrically defi ned cutting edge, which enables the maximum possible cutting speed of modern tool materials and coatings in the various workpiece materials. In relation to tool and mold making, the main focus is on the machining of easily machinable materials for model and electrode production (cutting speeds 800 – 2000 m/min-1) as well as the machining of tempered and hardened tool steels (cutting speeds 100 to 500 m/min-1). Modern fi nest carbide grade hard metals with coatings suited to the workpiece material
are used as tools. Typical tool diameters in tool and mold making range from D = 0.2 mm to D = 16 mm, whereby a maximum ratio of cutting length to diameter of L/D = 10 to L/D = 15 is possible.
With the EDM method, two charged electrodes in an electrically insulated fluid (dielectric) approach each other, until sparkover occurs between the tips, and, as a result, a plasma channel forms between the electrodes. The charge carriers, which are impinging on the electrode surfaces at high speed, convert their kinetic energy into heat, causing local melting of the electrode material on the contact surfaces between the plasma channel and the electrodes.
Due to the impinging of the charge carriers, a part of the melted electrode material is already vaporized or flung out of the existing crater. If, subsequently, the power supply is interrupted, the plasma channel collapses at high speed. The resulting low pressure increases the efficiency of the process, in which additional melted electrode material is removed from the crater by the high/low pressure effect.