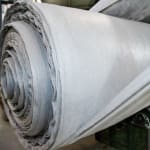
Inhouse recycling is nothing new, but it is worth taking a closer look when it comes to the complex recycling of high-strength PP nonwovens for civil engineering. The shredder-extruder combination from Pure Loop produces such high quality recycled pellets that the customer can now use a recyclate content of up to 10 percent in nonwoven production.
It is impossible to imagine the construction industry without geosynthetics. PP nonwovens, for example - mechanically bonded continuous fibres made from specially UV-stabilised polypropylenes - are often used in blanket form as barriers, screens and filters, and their strength extends the service life of construction projects. Whether for road construction, or as barrier on glaciers or against weeds - there are myriad applications.
This type of PP nonwoven can now be recycled using Pure Loop ISEC evo technology. The customer is TenCate Geosynthetics, part of the Canadian company Solmax. The European company with locations in Austria, France and the Netherlands is specialised in the development and production of geotextiles for modern civil engineering applications.
The edge trimmings and production rejects generated during manufacturing used to be recycled at the Linz site, but not fed back into the company's own production process. "It wasn't an issue at the time because the recyclate was sold. But in the meantime, it has become clear that reselling our valuable production waste is not an ideal solution, especially in view of the rising raw material prices. That is why we investigated the market to see which recycling technology would make it possible to produce recylate that meets our production quality," says Jürgen Gruber, Head of Marketing (Europe/Middle-East/Africa) at TenCate Geosynthetics.
"The demands on us were high," recalls Patrick Wiesinger, project manager at Pure Loop. "The PP nonwoven is highly tear resistant, which means its a very challenging recycling process. Our ISEC evo machine conserves the quality of the production waste really well during recycling, so we were able to achieve the specified increase in quality for the recyclates."
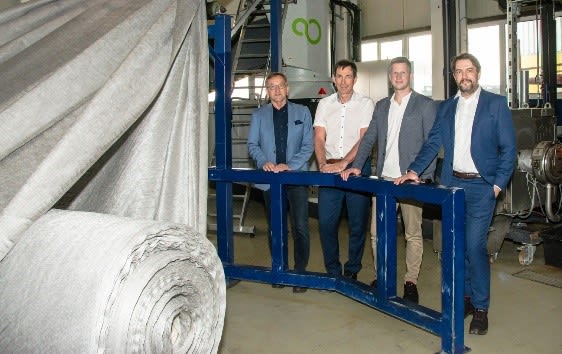
From the left: Günther Sebera (Head of Purchasing, TenCate Geosynthetics Austria), Gundolf Sabathiel (Plant Manager Linz, TenCate Geosynthetics), Patrick Wiesinger (Project Manager, PURE LOOP) and Jürgen Gruber (Marketing Director Europe/Middle-East/Africa, TenCate Geosynthetics)
Wide range of material shapes
Another advantage of Pure Loop technology is the wide range of shapes in which the production scrap can be delivered for processing. "At TenCate, one of the ways production scrap is delivered is on huge rolls. I'm talking about a width of up to 5 metres," emphas Patrick Wiesinger. "Our ifeed technology with double feed ram system and singleshaft shredder offers the ideal conditions for direct processing of these large rolls - and without the need for prior preparation of the input material by employees before the material is fed into the recycling process." With the ISEC evo recycling machine TenCate can now manufacture its high-strength PP nonwoven product with a recyclate content of up to 10 percent.
"Thanks to the Pure Loop technology, it is now possible to return the high-quality recyclates directly to production. It makes sense in terms of cost effectiveness and it is an important step for us within the company in view of the circular economy that the industry is striving for," explains Jürgen Gruber. Currently, production waste from the sister site in France is being repelletised for production, while waste from the subsidiary in the Netherlands is being processed at the Pure Loop plant in Linz for test purposes. "We produce many other special plastics in addition to this PP nonwoven. If we achieve the same high quality of recycled pellets, then we are open to using the Pure Loop technology for other materials as well," says Jürgen Gruber.