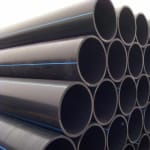
The PE100+ Association celebrates its 20th anniversary this year. Founded in 1999 to assure consistent quality at the highest level in the production and application of materials for PE100 pressure pipes, it is just as relevant today as it ever was.
Member companies of the association offer high-density polyethylene (HDPE) for pressure pipes for gas and water with excellent hydrostatic strength that last for decades, combined with high resistance to slow crack growth and to rapid crack propagation. Performance targets set by the PE100+ Association surpass standards around the world for PE100 materials.
Meeting an important need
The PE100+ Association was founded in 1999 by three European polyethylene producers a few years after the very first introduction of PE100 in the market. Today, it comprises 13 companies from around the world (in China, Korea, Thailand, the Middle East region, as well as Europe), and the number of members continues to grow. An advisory committee of non-affiliated independent experts that are active across the pressure pipe value chain supports the Association.
The members have made a voluntary commitment to regular quality checks - at least on annual basis - in cooperation with an independent administrator Kiwa and several other independent test labs across Europe. Kiwa asks for batches of materials from material suppliers on a random basis. Pipes are usually made in members’ own processing centres and sent to independent institutes for testing. An important principle of the PE100+ Association is that certified PE100 materials are listed as ready-made black or coloured and fully formulated compounds, rather than supplied to pipe makers in a natural base resin form that is coloured using masterbatch and other additives at the pipe extrusion line.
The PE100+ Association monitors the decisive test methods for PE pressure pipes in round-robin tests, which involve it checking to make sure that the independent test institutes verifying pipes are performing tests in ways that make them comparable. “We need to be sure that for any given material, different test institutes provide the same outcomes within a certain bandwidth, this information we also provide to the ISO committee who is responsible for the update of test method standards” says Hans Pierik, President and Chairman of PE100+ Association, and Business Manager at SABIC.
Today, not only the pipes, but all the fittings and all the tools used to install pipes are organized to comply with PE100. “It’s not just about material quality but also about pipe diameter and thickness based on the pressure resistance of the material,” continues Pierik. “If all pipes have the same dimensions, it doesn’t matter if the pipe comes from Producer A and the fitting from Producer B - everything fits together.”
Adapting to new pipe laying techniques
Although members are all suppliers of HDPE, the PE100+ Association communicates with the full value chain, including converters, installers and standardisation bodies, with whom it has an active dialogue on such matters as product criteria for new pipe laying methods.
One of these covers PE100-RC (RC stands for Raised Crack resistance, see prEN1555-1), covering materials for pipes with increased slow crack growth resistance that makes them more durable for alternative installation methods like trenchless installations, renovations like relining, pipe bursting or sandless bedding of pipes.
“The move from traditional installations in PE100 to trenchless installation with PE100-RC should enable major system savings,” says Norbert Jansen, Treasurer of PE100+ Association and working at Borealis. “It’s not just about the cost of the material and pipe extrusion. Most of the costs come during the installation, for example the cost of closing a road, digging the trench, laying the bedding and then the pipe, covering the pipe and maybe resurfacing the road. With trenchless pipe installation, you can obtain considerable savings in infrastructure.”
Faster ways to check for long-term properties
At present, there is no uniform resin or pipe requirement for resistance to slow crack performance. The PE100+ Association is acting as a driving force for change, working on development of new and much faster – but still reliable – accelerated test procedures. These include a Strain Hardening Test (SHT) originally developed by SABIC and which is now an ISO standard ISO18488. Furthermore an accelerated version of the FNCT (Full Notch Creep test ISO16770) and an accelerated version of the NPT (Notch Pipe Test ISO13479) was promoted to be used. Last, but not least the CRB test (Cracked Round Bar test ISO18489) was selected for the revision of EN and ISO standards for PE pressure pipes.
The PE100+Association unveiled in 2017 an online “No Dig” technical guide. This identifies the properties, benefits and applications of PE100 in trenchless techniques for use by designers and decision makers, enabling them to decide which methods are applicable to a specific project.
“The PE100+ Association continues to grow and to evolve as it adapts to changes in technologies and markets,” says Hans Pierik. “I believe we are now an invaluable link in HDPE pressure pipe value chain, all the way through to consumers who demand reliable, consistent and safe delivery of gas and water to their homes. We have come a long way in 20 years, but we still have work to do.
“We see many opportunities in emerging and developing countries, for example. In China, the new national standard GB/T 13663 for PE piping systems for drinking water applications was released this year, and the PE100+ Association has been very active in the country promoting the benefits of PE100 pre-compounds for pressure pipes, and developing new tools and services for the pipe value chain.”
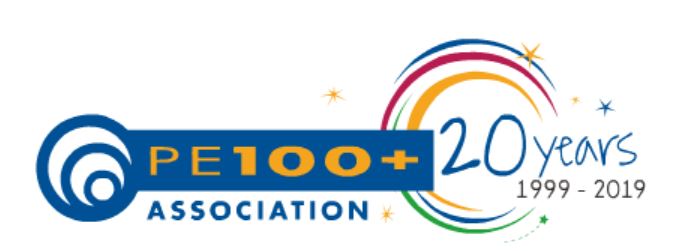