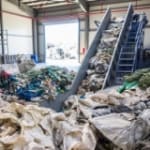
Mr Weber, does Herbold Meckesheim gain when raw material prices rise all over the world?
If raw materials become scarce or expensive, there is increased demand for recycling technologies and hence for our plant and machinery too. At such times, people also consider reprocessing products that used to be thrown away. Waste raw materials, such as trimmings from plastic film production or runner loss from injection moulding, are quite easy to recycle. If the materials are heavily soiled, it is more difficult. Then the effort and expense required for recycling are much greater. But that is where we see greater business opportunities. A lot of firms can do basic recycling, and there is keen competition from Asia in particular. But not many have mastered sophisticated recycling as well as we have.
How much more expensive do raw materials have to become?
The difference between the costs of raw materials and recycled material has to be large enough to create demand for sophisticated and expensive recycling technologies. For example, a tonne of film made from new materials costs between 1,200 and 2,000 euro. You have to pay between 180 and 250 euro for a tonne of reprocessed film.
In what fields is the reprocessing of soiled waste particularly worthwhile?
Films for agricultural use represent a growth sector, for covering large areas such as fields or silage. One need only think of the enormous areas of film used to cover fields of asparagus. These films are heavily soiled by loam, plant residues and manure. This dirt clings to the film and after a while it is hard to wash off. Asparagus films are generally rolled up and reused once or twice. But then they are so badly damaged that they have to be changed.
What do your machines do with the soiled film?
There are several stages to the process. First there is coarse grinding, then several washings. Finally, the material is separated by centrifugal force in a hydrocyclone and then thickened in an agglomerator so that a free flowing granulate comes out at the end.
Can raw material be replaced by 100 per cent recyclate?
It depends on the quality required. But basically thirty to fifty per cent of the raw material can be replaced by recyclate even with respect to the highest quality requirements. For less demanding applications, even one hundred per cent regranulate can be used.