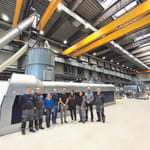
Premiere at Erema: the new Intarema 2325 sees the world's leading manufacturer of plastics recycling systems grow its post-consumer series to enter a new dimension in recycling. The Intarema 2325 T-VEplus RegrindPro with laser filter is the largest system ever built to recycle polyolefin regrind and marks a milestone in the very latest recycling technology.
As the demand for recycled plastics increases, so does the need for larger recycling machines. This is an industry where Erema can draw on a wealth of proven experience. In the PET sector, the machine manufacturer has already implemented several projects with large-scale systems of this magnitude featuring their Vacurema technology. Now the company is following that up in polyolefin recycling. The new of Iintarema is Erema’s response to market demand. "New legislation and the voluntary commitment of major product brands mean that in the future, our customers will need to process an increasing volume of plastic waste to make high quality recycled pellets without any compromises," says Markus Huber-Lindinger, Managing Director at Erema. "The Intarema 2325 is our answer to this need."
More recycled pellets per hour
The Intarema generation of machines is Erema's flexible series for handling a wide variety of feed materials. Available in 13 s for film and 9 s for regrind applications, the Intarema range covers a broad spectrum. The new 2325 model with a preconditioning unit (PCU) diameter of 2.30 metres and an extruder screw with a diameter of 250 millimetres enables the production of high volumes of high-quality recycled pellets using a single machine. "With a throughput of over 4,000 kilograms per hour for PO regrind, the Intarema 2325 sets new standards in terms of performance and efficiency," emphasises Huber-Lindinger. The system also impresses with its compact footprint in contrast to its high throughput capacity.
Consistent processes combined with a high level of automation
The plant is packed with innovative technology. The proven key principle of the TVEplus Counter Current system lies in melt filtration upstream of extruder degassing. This makes it possible to produce recycled pellets of impressively high quality, meaning that the proportion of recycled plastics used in the final product can be significantly higher than with lower-quality recycled pellets. "Our extensive trials with around 500 tonnes of material have shown that the Intarema 2325 impresses with high-quality recycled pellets at high throughput rates, all within a very stable process," says Sophie Pachner, R&D Manager for Process Engineering at Erema.
Like all Intarema systems, this one is also equipped with patented Counter Current technology. The plastic material moves through the preconditioning unit in the opposite direction to the extruder screw, ensuring a consistently high output over a wide temperature range. This system, combined with a high degree of automation thanks to the intelligent Smart Start user interface and energy-saving ecoSave technology, makes the Intarema series particularly user-friendly and efficient.
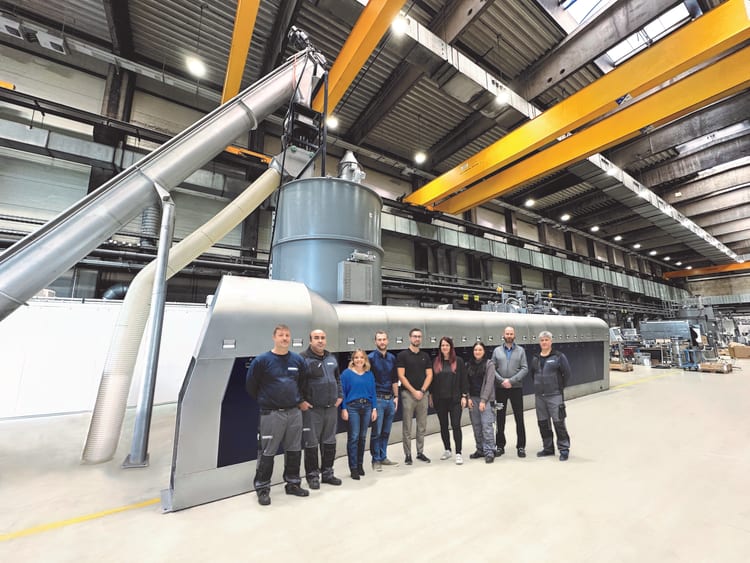
Largest laser filter ever
"We are convinced that the Intarema 2325 is capable of achieving very high throughputs even with challenging process parameters," says Huber-Lindinger. "This machine is further proof of our company's outstanding engineering capabilities and our willingness and expertise to solve major challenges in plastics recycling."
Many of the specially built, large-scale components were installed and matched together for the first time during this project, such as 690-volt motors and the largest laser filter system ever built by Erema. The 2/406 Quattro Laser Filter has a total filter area of 7,800 square centimetres and contributes to the high stability of the plant thanks to its robust design and precision filtration. The control panel array is also something new. At 12 metres long, the electrical container is imposing, but it is compact relative to the of the machine. The well-thought-out configuration makes prior installation, transport and maintenance work particularly straightforward.
Machine available at short notice
Erema offers machines for all applications, from small through to XXL s. From small systems for production waste with a throughput of around 100 kilograms per hour to large-scale PET systems with an output of 6,000 kilograms per hour, the company’s product range covers the whole spectrum. "The Intarema 2325 fits perfectly into our wide product portfolio and enables us to respond even more specifically to the needs of our customers," says Huber-Lindinger.
The Intarema 2325 is available immediately and can currently be purchased through Erema's Fast Track scheme, which offers selected machines with particularly short delivery times. More information is available online at https://www.erema.com/en/fast-track-machines